The State of Carbon Neutrality in the US
By: Chris Hoyle, Sr. Vice President-Technical Director; Brian J. Naveken, Mgr. of Technology & Administrative Supervisor of Information Technology Department
Introduction
Net zero emissions refers to the state in which total greenhouse gas emissions, carbon dioxide (CO2), going into the atmosphere is balanced by their removal out of the atmosphere. This can be achieved by reducing emissions or removing the CO2 through natural or artificial means or a combination of the two. This is becoming more imperative with the increase in the production of greenhouse emitters. For example, the United States alone, there has been an increase in the production of natural gas of approximately 79% since 2010 along with crude oil (Figure 1).
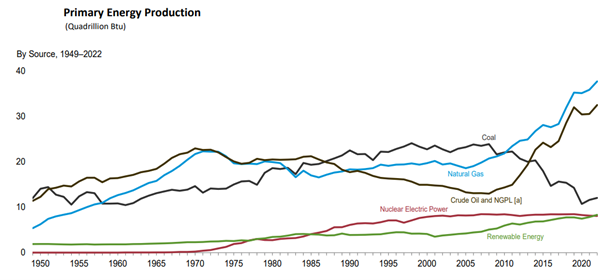
Figure 1: U.S. Energy Information Administration/ Monthly energy review (February 2024)
Within the glass industry, the primary source of CO2 is from the combustion of natural gas, electricity produced from non-green sources, primarily natural gas, and the reaction of the carbonated forms of batch materials (Figure 2). With natural gas and carbonated materials being the most economical fuel source and raw materials to use, what is the current state of carbon neutrality in glass and where can the industry head?
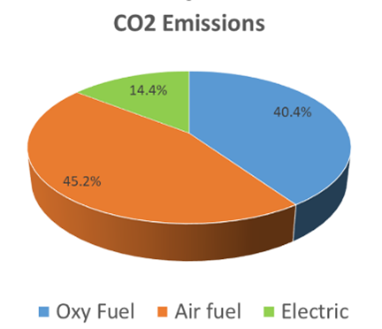
Figure 2: CO2 emissions by furnace type
Paths to Carbon Neutrality for Glass Manufacturing
Currently, there are basically four paths to carbon neutrality for glass manufacturing. These being:
- Energy Efficiency
- Batch Modifications – Increased use of cullet and elimination of carbonate materials
- Carbon Capture/Sequestration
- Alternative Fuels - Hydrogen, Biogas, Blends, Electricity
These paths are not mutually exclusive, they can be combined to increase the reduction in CO2 emissions.
The first one on the list is nothing new. Glass producers have been in a constant state of improvement when it comes to energy improvement. Previously, this had nothing to do with carbon emissions but to do with reducing their cost per ton of glass. Energy efficiency is nothing new and there isn’t a plant that isn’t continuously trying to improve their efficiencies. Simply put, this route is lower your energy consumption, lower your carbon footprint.
Interestingly, the fourth item, alternative fuels, does not address CO2 emissions from the batch. So, carbon capture would still be required and/or the use of carbon credits. In this article, the economics, more specifically the operating expense (OPEX) considerations are going to be limited to alternate fuels, specifically hydrogen (H2) and batch materials
Batch Modifications
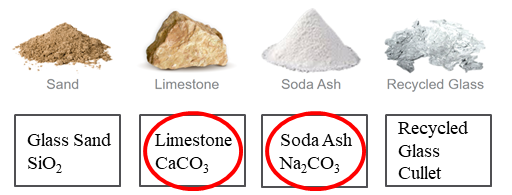
Figure 3: Basic batch materials of Soda Lime Silicate glass
At 20% cullet approximately 35% of CO2 emissions from the production of glass is from the melting of the batch materials and to date has not received the attention that emissions from fuel has gotten. Other CO2 emissions by cullet percentages are represented in Figure 5.
In a basic equation for the production of glass,
SiO2 + Na2O + CaO → Soda Lime Silicate Glass
there contains no carbon dioxide (CO2) product formation. The formation of CO2 is a product of using the carbonate forms of the Na2O and the CaO more commonly known as soda ash (Na2CO3) and limestone (CaCO3). The resulting equation now becomes,
SiO2 + Na2CO3 + CaCO3 → Soda Lime Silicate Glass + CO2
Figure 4 shows some typical volumetric (normal) and mass flows of exhaust CO2 due to batch.
There are two main reasons why the carbonate form of the raw materials is used. These being the abundance of the raw materials, which also results in a lower cost, and secondly the melting of batch takes less energy than their oxide forms. By using soda ash and limestone, this reduces their respective batch material cost by approximately 4-5 and 1.5-2 times (Figure 6). Alternatively, batch materials from recycled sources, such as water treatment waste and fly ash, can be used but this will only reduce the carbon footprint by 4-10%. To get to complete neutrality, carbon capture/sequestration would still be needed.
There is research on producing soda free glass. This glass contains no soda or sand in the raw batch and utilizes 50% cullet. The test results are positive reporting approximately 10% emission savings related to batch.
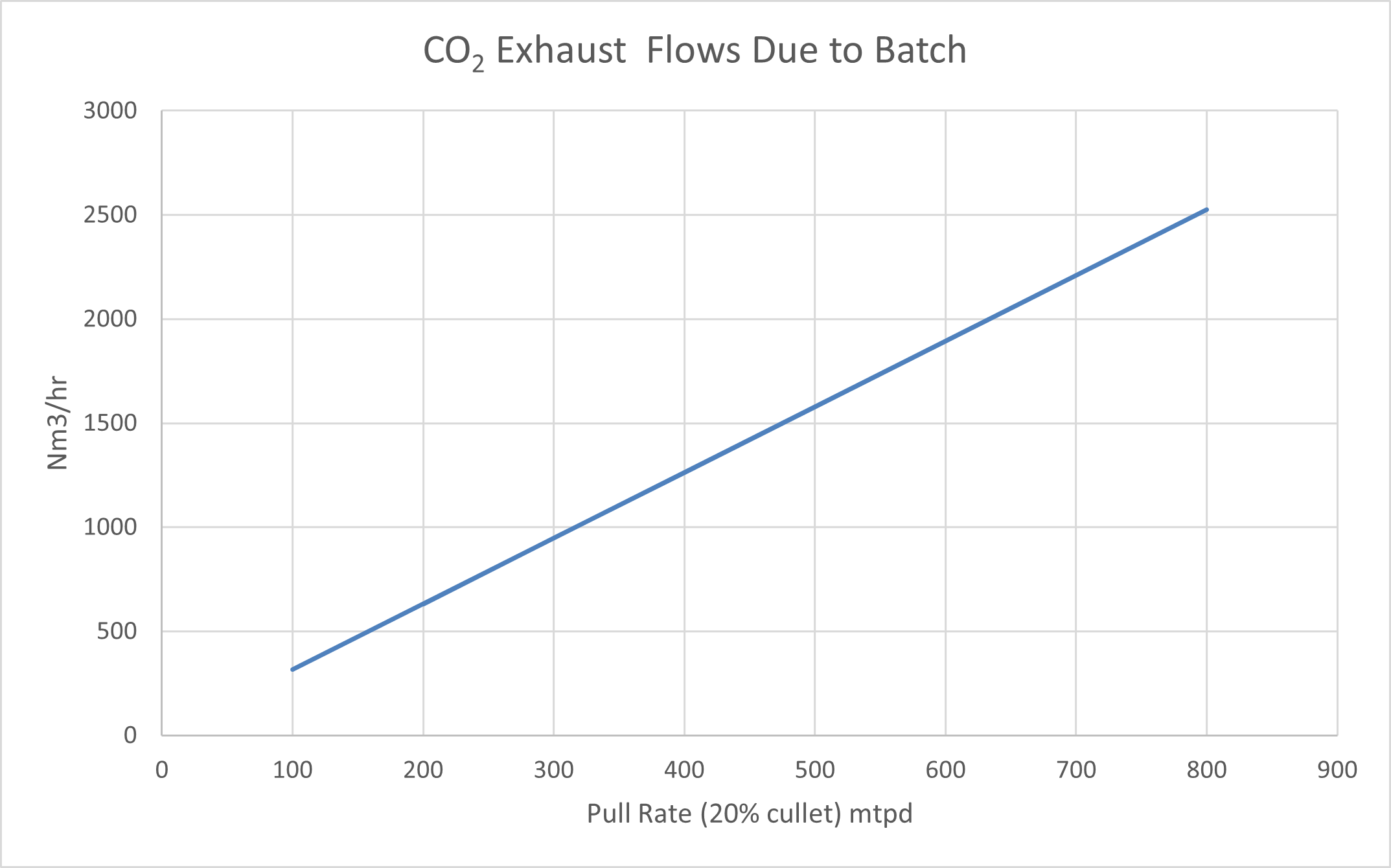
Figure 4: Carbon Dioxide flows in exhaust due to batch materials
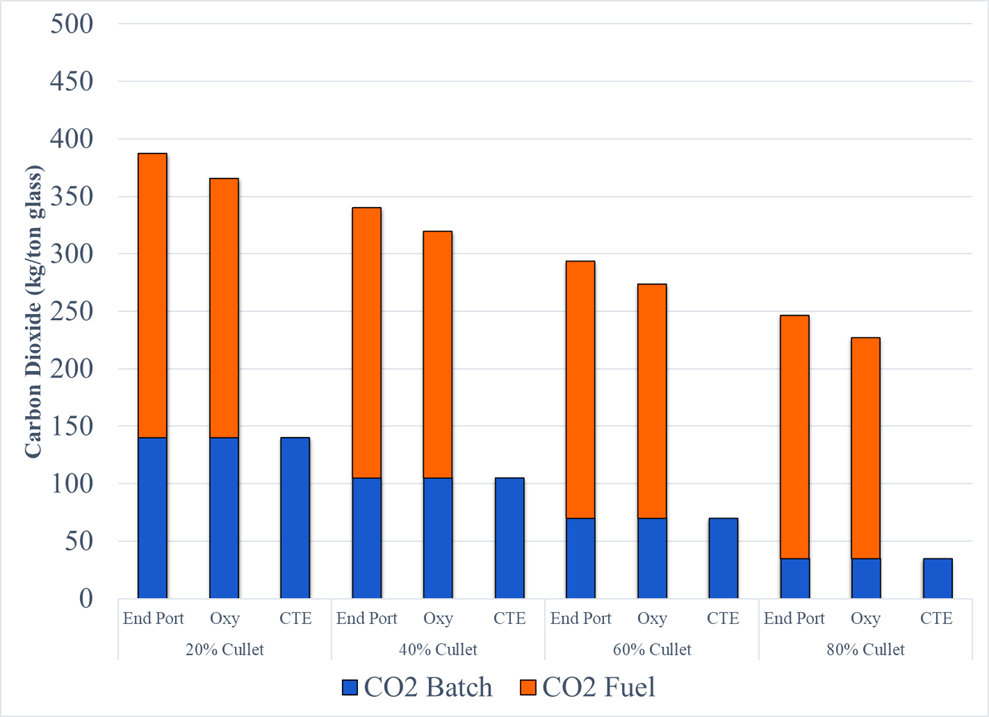
Figure 5: Carbon Dioxide Emission from glass (batch) and fuel by furnace type and cullet level

Figure 6: Summary of increased cost due to raw material and melting energy
Carbon Capture/Sequestration
Carbon sequestration is the long-term process of capturing and storing atmospheric carbon dioxide. The idea is to store the carbon dioxide in stable forms within solid and dissolved media. In order to accomplish this, CO2 capture technology is required within a plant or a separate facility. This raises additional questions. What do you do with it? How do you store CO2 and for how long? And most of all, what is the added cost?
There are three main types of carbon sequestration: geological, biological and technological.
Geological
Geological sequestration is storing CO2 underground. The key word here is storing. It is not converting. The ideas here are:
Biological
Biological sequestration is storing and converting CO2 through plants and oceans. Within plants it is the natural photosynthesis process. As part of this process, the plant soil can store the CO2 as carbonates. However, the plant soil organics can only store carbonates for a few decades. For this reason, studies are being done to accelerate this forming process by adding crushed silicates to the soil in order to extend the storage period.
Oceans are CO2 converters. This is primarily due to plankton, seaweed and algae.
Biomass can be used in factories for carbon capture and storage. The carbon sequestered by the biomass would be buried directly. This mimics the natural processes that create fossil fuels.
CO2 can also be pumped into ponds that are intentionally filled with bacteria and algae.
Lastly, certain areas of the country are also more conducive to natural CO2 conversion due to forests, grasslands and farming. Within these areas of the country there are subsets that are even more conducive to natural conversion.
Technological
The use of innovation technologies are being researched to use CO2 as a resource. Some of these technologies are:
Currently, carbon sequestration is extremely expensive and energy intensive. A carbon capture plant will cost more than the glass plant that it will support and is not a viable solution with today’s technology. An example of a carbon capture plant can be seen in Figure 7.
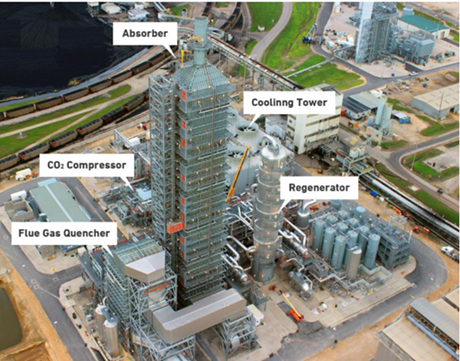
Figure 7: Example of a Carbon Capture/Sequestration Plant
Alternative Fuels
When looking at carbon neutrality, hydrogen (H2) looks to be the most viable candidate, and this can be seen in the research and the billions of dollars in potential funding for hydrogen hubs and infrastructures. In the United States alone there is a Department of Energy funding opportunity of $8 billion for the five (5) year period encompassing fiscal years 2022 through 2026 for the development of regional clean hydrogen hubs that demonstrate the production, processing, delivery, storage, and end-use of clean hydrogen. This concept is presented in Figure 8.
The basic equation for the combustion of natural gas using air or oxygen is,
CxHy + zO2 → xCO2 + (y/2) H2O
Natural gas is primarily made up of methane which burns as,
CH4 + 2O2 → CO2 + 2H2O
Now, if we look at hydrogen, the CO2 product gets eliminated.
2H2 + O2 → 2H2O
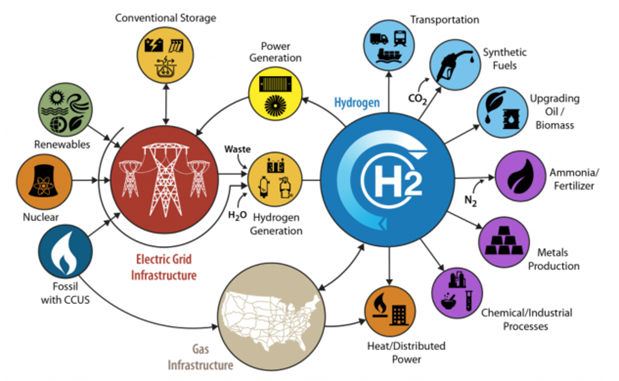
Figure 8: H2@scale U.S. Department of Energy (www.energy.gov/eere/fuelcells/h2scale)
Perfect! The H2 combustion eliminates of 100% of the CO2 from the gaseous energy source for melting and refining glass (note: all electric melting does the same). But let’s look a bit closer. The heating value of a typical natural gas is ~36.73 MJ/Nm3 as compared to hydrogen’s ~10.78 MJ/Nm3. What this means to glass melting is:
Figure 9 shows the comparison of a container and float furnace using air-gas or oxy-fuel and replacing the fuel type with hydrogen with all other inputs remaining the same.
The economic practicality is constantly changing and will continue to change due to energy prices and the processes used to generate hydrogen. Taking the first bullet point from above, in order to get the same melting energy from hydrogen you need to increase the volumetric flow of hydrogen by three to three and half times. If hydrogen cost gets comparable to natural gas on a volumetric basis, which currently it is two to three times higher, one’s energy cost would still be triple due to the increased volume of hydrogen needed. To put the volume of hydrogen into a bit more perspective, for a float furnace to convert their port 0 oxy-fuel burners to hydrogen would require five times more hydrogen than what they use to operate their tin bath. However, by 2050, the natural gas economic advantage may disappear with the addition of carbon taxes.
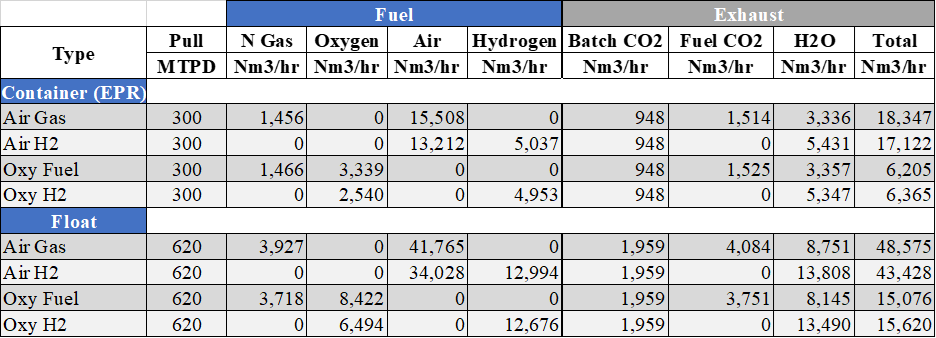
Figure 9: Fuel flows and specific species exhaust flows
Technical Feasibility of Hydrogen in Glass Furnaces
The first questions for the success of hydrogen combustion is how will the hydrogen be generated, transported, stored and ultimately burned in existing glass furnaces? Or will all new furnaces designs be needed? Or just modifications to existing furnaces?
Some of the considerations for furnace conversions from natural gas to hydrogen are:
Side Note – Electrical Furnaces
With all electric furnaces CO2 emissions are eliminated to same degree as hydrogen combustion and has been a production proven and economical method of melting glass. The biggest drawback is glass quality but with the same degree of effort and innovation that hydrogen combustion is receiving, the fining/refining issues should be able to be overcome.
Conclusion
Carbon emissions from batch materials is significant. At 20% cullet it accounts for approximately 35% of the CO2. Non-carbonate forms of soda ash and limestone will need to addressed while considering economic and supply considerations. Carbon sequestration is extremely cost prohibitive. Using hydrogen as an alternative, the price of hydrogen needs to be reduced considerably in relation to natural gas.
All electric furnaces from a fuel standpoint produce no CO2 like H2 and have been production proven for many years by the leaders in all electric melting, The TECO Group. More innovation into the refining and fining of glass using all electric may ultimately make the most economic sense.
Internationally there is a considerable decarbonization effort going on within the glass community as well as other industries. Hydrogen trials in glass furnaces have begun and will continue. Refractory companies are conducting tests for increased water content in the exhaust and burner companies are developing new designs for hydrogen combustion. The challenges to decarbonize glass production are numerous and demand innovation along multiple paths, from raw materials to adaptation of hydrogen combustion, to advances in all electric melting. The TECO Group and its seven (7) companies are uniquely positioned to solve clients’ issues, in this case decarbonization, by delivering innovative solutions that creates value within a framework of managing risk.
Add a Comment