Design-Build, A Better Way – Part 1
By Doug D. Burgoon, Vice President of Operations
This is the moment you have been dreading for months. The owner has summoned you to his office for an update on the company’s biggest project. You know all the questions he is going to ask because the bad news has been slowly building for months now, and you have been at the center of the storm. Since the beginning, you have witnessed the gradual unraveling of the project like it was happening in slow motion. Missed deadlines; unexpected “extras” from contractors; an inflated budget. The end date of the project has slipped – not once, not twice, but incessantly. So much so that nobody believes you anymore. Right now, you’re thinking back to that design-build seminar that you attended before the project started and wondering how this project could have turned out differently. Good luck – you’re going to need it.
Executives in the industry already know that primary glass manufacturing is a capital-intensive endeavor. As companies deal with the unrelenting pressure to reduce capital cost, more are discovering that project delivery concepts matter. In the search for the lowest Total Cost of Ownership (TCO), capital delivery is commonly overlooked, but its impact can often mean the difference between business failure and success.
Now is the time for the glass industry to modernize its thinking with respect to capital delivery. In particular, Design-Build (DB) project delivery is attracting more adherents as executives discover its benefits. The first portion of this two-part paper will break down exactly what DB is and explain why it is so effective. Part 2 in the following issue, will offer suggestions on how to increase its use in the glass industry.
Design-Bid-Build, The Old Standard
Most glass-making professionals are familiar with the Design-Bid-Build (DBB) project delivery methodology. It is the dominant delivery method in the business world, and it is relatively straightforward. In the DBB model, there are three main sequential phases:
- The design phase;
- The bidding (or tender) phase;
- The construction phase.
The Owner either performs the design work in-house or negotiates with an engineering design firm to prepare drawings and specifications under a design services contract. Subsequently, separate contracts for construction are negotiated through engagement with a contractor through competitive bidding. Under this arrangement, the Owner warrants to the contractor that the drawings and specifications are complete and free from error, which means the Owner bears the risk. The selection process for DBB is usually based on negotiated terms for the design contract and lowest bid for the construction contract.
Design-Build, A Better Alternative
By contrast, the Design-Build (DB) form of project delivery is an advanced system of contracting whereby one entity performs both the engineering and construction under one single contract. Under this arrangement, the DB contractor warrants directly to the Owner that it will produce design documents, which means the design-build contractor bears the risk, as opposed to the Owner. The selection process under DB contracting can be in the form of a negotiated process involving one or more contracts, or a competitive process based on some combination of price, duration, and proposer qualifications. Portions of the overall design or construction work can be performed by the DB entity or subcontracted out to other companies that may or may not be part of the DB team.
In this method, the design and construction services are contracted by a single entity known as the Design–Build Contractor.
Design-Build in Motion
Interestingly, DB application is much more common outside the glass industry. This is most likely attributed to the fact that our industry is inherently conservative and risk averse. However, we are seeing more glass companies incorporate the model as its successes become more apparent. Furthermore, there have been numerous studies that confirm the benefits of the DB project delivery. For example:
Project Metric |
DB vs. DBB |
Unit Cost |
6.1% lower |
Construction Speed |
12% faster |
Delivery Speed |
33.5% faster |
Cost Growth |
5.2% less |
Schedule Growth |
11.4% less |
“Comparison of U.S. Project Delivery Systems,” Mark Konchar & Victor Sanvido, Journal of Construction Engineering and Management, Vol. 124, No. 6 (1998), pp 435-444.
While the data varies, similar studies by other researchers all point to the same conclusions; DB projects outperform other project delivery methods when looking at common project metrics such as:
- Cost performance;
- Schedule control;
- Number of change orders;
- Quality of end product.
The Value of Design-Build
So, why is DB so effective? Well, firstly, it eliminates “finger pointing” between the engineering and construction teams. We all know how frustrating it can be when two separate entities attempt to impose their own individual ideologies, company cultures, and style of communication on one another. Of course, there are instances of two teams from different businesses working cohesively, however, DBB tends to present more opportunities for the proverbial ball to be dropped.
On the other hand, in a DB model, both parties are under the same umbrella, which means there are built-in incentives to anticipate problems before they become issues. Engineers can directly consult with construction personnel as to the practicality and constructability of their designs, while construction personnel can have input during the design phase. The chance for miscommunication is reduced considerably.
Secondly, the DB model offers more cohesion when considering constructability and modular design, and as a result, ensures efficient use of construction resources later in the project. It is common for construction crews to use different methods to achieve the same result. For example, in the glass industry, some construction companies use robots to assist with demolition of furnace refractories, while others use excavation-style equipment. Both methods, when done by experienced crews, will achieve the same result with the same productivity. When working under the same umbrella as the modular design team, the construction team can better assess which method is more suitable to the particular project at hand.
Let’s also look at it from another angle. In assembling a complex steel structure, in some instances it makes more sense to assemble it in a more controlled environment like a fabrication shop. In other situations, due to uncertain field conditions, it may be more prudent to assemble it in place. The engineering needs to match the method chosen in order to ensure success. It is just this type of collaboration between construction personnel and engineering staff that amplifies the benefits of constructability reviews in the DB process.
Front End Loading (FEL) is a project management philosophy that emphasizes early project definition. It starts by defining project goals and functionality, progresses through option analysis, and typically results in a near-detailed scope of work. The more thoroughly a project can be technically defined, the earlier it can be broken down into actionable tasks. As a result, the overall schedule can be compressed. Considering more options during the FEL phase reduces the uncertainty and duplication introduced by late stage changes during the project. As shown in the illustration below, the best time to impact project costs is before the engineering and design starts. Coincidentally, this is also when the rate of spending is typically lowest.
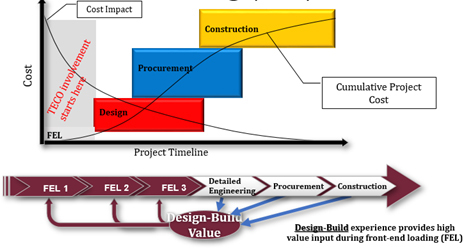
While FEL typically refers to the upfront planning process, a project can also be front end loaded by accelerating procurement and construction activity in the early phases of the project. For example, purchasing material and equipment early may help avoid inflationary increases by suppliers. Also, beginning process equipment or steel erection while the building envelope is still open can dramatically increase construction efficiency.
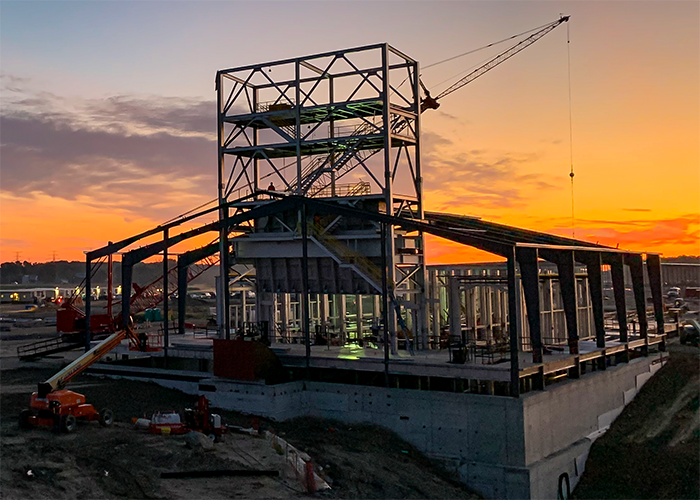
DB models also eliminate interfaces. Interfaces can be discontinuities in the project where information can get lost, design intent can get misinterpreted, and where most surprises tend to happen.
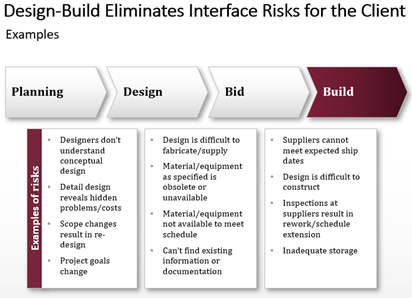
Combining design and construction responsibility opens up many more opportunities to perform activities in parallel, further contributing to compressed schedules, which ultimately means much of the project overhead is reduced. For example, the need for field equipment that is typically rented, such as cranes, forklifts, construction trailers, etc., is time-curtailed, resulting in cost savings.
Shorter schedules also translate into smaller windows for scope changes. As any project manager will tell you, late stage changes are disproportionately costly because they often mean changes to work already completed as well as costly knock-on effects.
In summary, the benefits of the DB project delivery method simply cannot be denied. Improved communication, the elimination of finger pointing and interfaces, the empowerment of constructability processes and modular design, better (and more) FEL, and schedule compression, as well as the opportunity to minimize scope changes, reduce cost and project overhead through more efficient construction processes will assuredly make for less missed deadlines, fewer unexpected extras and no more budget-crippling surprises. With all of these advantages, why would any decision maker decide not to employ the DB project delivery method? This question, as well as suggestions to increase its use in the glass industry, will be the focus in Part 2. Stay tuned.
Add a Comment