Non-destructive control of fused cast AZS for high-quality glass melting - Part 1 of 2
How can efficient non-destructive control of fused cast AZS support high-quality glass melting?
Authors: Isabelle Cabodi, Zi Kang Low, Pierrick Vespa – Saint-Gobain Research Provence, Cavaillon, France
Mélanie Allen Larut, Michel Gaubil, Frédéric Pomar – SEFPRO, Le Pontet, France
For more information, don't hesitate to contact us.
Latest trends in glass furnaces, towards clearer glass and electrification, have underlined the importance of quality controls on AZS to extend the furnace lifetime while maintaining good glass quality. The purpose of this article is to describe three non-destructive control methods on refractories and their impact on furnace properties. We will describe how block color control is crucial to obtain good glass contact properties (blistering and exudation), how an optimized block filling, controlled thanks to radar waves, is required to maximize furnace lifetime, and how optical tools enable reliable joint face analyses to ensure limited corrosion inside joints. Finally, we will demonstrate that thanks to the ongoing digitalization of the refractory manufacturing process and through these new measurements, SEFPRO will be able to offer refractory solutions to support the transition of glass melting technology towards low-carbon processes and more severe conditions for refractory materials.
Several trends impacting the corrosion of AZS tanks have been identified in glass furnaces. The first one, related to the reduction of environmental impact is the electrification of glass furnaces: using strong electrical boosting or hybrid furnaces triggers major changes in thermal profiles and therefore corrosion profiles. The second one is the move towards clearer glass, increasing temperature and corrosion at block bottom. These trends are occurring in parallel to longer campaigns. In this context, the quality of blocks becomes critical to support these challenges.
AZS fused cast refractories are not all equivalent in terms of quality. Three main properties have been identified that could significantly change refractory lifetime and glass quality: block color (product oxidation), filling, and microstructure.
SEFPRO has developed several non-destructive tools and controls (NDE) to monitor this quality and to develop the most suitable product for each application. We will detail developed and currently under development NDEs and explain the link between the measured properties and their impact on refractory performance.
Impact of AZS color and control protocol
AZS fused cast refractories contain a small quantity of impurities inside their glassy phase, mainly iron or titanium ions, for a few tens of ppm. These ions are responsible for the color of the blocks, and are a reliable indicator of the oxidation state of the product. Indeed, they are multivalent: if the product is well oxidized, only ferric ion (III) can be found inside the product giving a light red color, whereas non-optimal oxidation will let ferrous ion (II) or iron (0) inside the glassy phase, giving a greyish product. The link between color and oxidation of impurities has been proved thanks to XANES measurements. If the product is reduced, some dissolved gazes and remaining carbon can also be found in the material. This small quantity of reduced impurities can then have an impact on two major properties, exudation and blistering. The link between color and oxidation state of present species can be summarized in Fig 1.
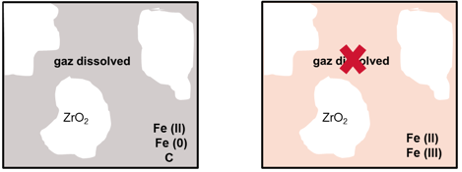
Theory of Color Measurement
As it has just been described, the color of a refractory gives a major clue in terms of its redox state and the quantity of gazes dissolved. Nevertheless, perceived color is strongly observer-dependent and lighting-dependent. Hence, a standard scale has to be used to describe color, measured by a reproducible protocol.
SEFPRO is using spectrophotometry thanks to reflection: a standardized flash lamp is illuminating the measured sample, and thanks to an integrating sphere, three sensors, reproducing eye cells sensitivity are measuring red, green, and blue levels. L*, a*, b* scale is then used to quantify the color, as described in Fig 2.
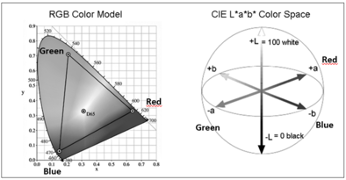
Three properties can be measured by this scale: Lightness (L*), and chromaticity values (a*, b*). The Chroma (C*) is defined as the distance between the color of a sample and the projection of this color on the grey axis (vertical L-axis):
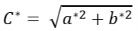
Hence, an oxidized product will have a high lightness (towards 100) and a slightly reddish color. Its Chroma should be high enough, depending on the lightness value.
Color and blistering properties
As previously detailed, a greyish material contains reduced species such as Fe (II), Fe (0) or C. In soda-lime glass, with sulfate-based fining, sulfur dioxide blistering could be triggered because of the contact with reduced iron, following the equation:

This transient blistering will be longer for a greyish refractory, containing more reduced iron, than for a well-oxidized product. To illustrate this phenomenon, a video-recorded blistering trial was performed at 1350°C. A crucible of 50 mm diameter and 50 mm height with a recessed area of 30 mm diameter and 30 mm height is installed inside a furnace with a small opening at the top. Soda-lime glass cullet is put inside this crucible. Thanks to a mirror and suitable filters, the behavior of blistering directly inside the crucible can be monitored. Set-up is described in Fig 3.
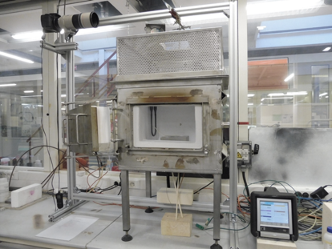
With this set-up, we have demonstrated that transient blistering lasts 8 hours for a well oxidized AZS 36 (L=89.3 and C=6.1) whereas it lasts 24 hours for a grey AZS 36 (L=83.2 and C=8.0). Bubbles are also larger in the case of the reduced product. Fig 4 shows blistering after 1 hour and 9 hours of trial:
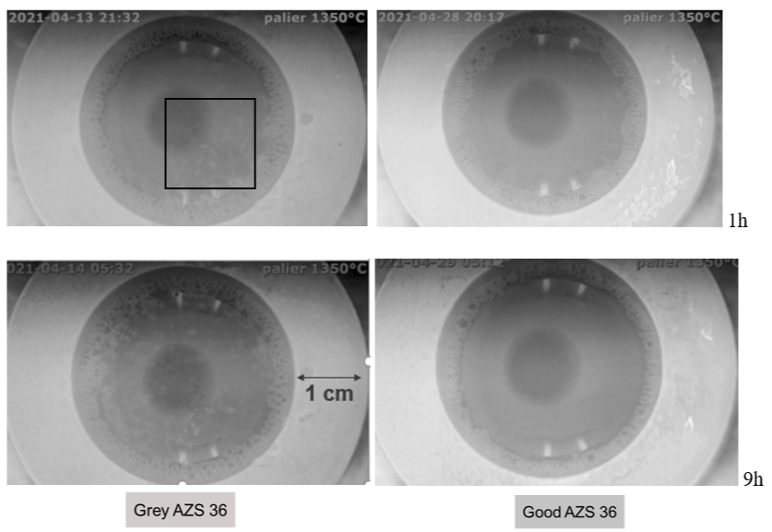
With gradual corrosion, the thermal gradient moves inside a block in a real furnace. Hence, these redox reactions will resume regularly, creating new bubbles: a well-oxidized product is crucial to increase yield, reducing bubble defects in glasses.
Color and exudation properties
Exudation of refractory is the quantity of glassy phase contained inside the refractory which comes out of the product when the temperature is increased because the glassy phase has become more fluid/liquid. Two main forces drive this phenomenon:
- Zirconia skeleton shrinkage during phase transition: the 4% contraction triggers an increase of pressure in the glassy phase. It occurs for all AZS refractories.
- Pressure from dissolved gazes: a reduced material will contain more dissolved gazes, coming for example from a poor melt fining or from oxidation of sulfur and carbon. With increasing temperature, the quantity of gazes will increase (by impurity oxidation), whereas their solubility could decrease, generating additional pressure on the glassy phase.
As such, a grey product, with more reduced species, will exudate more than a well-oxidized product.
Two tests are used to measure the exudation of AZS products:
- Bar exudation: samples are cylinders of 24-mm diameter and 100-mm height suspended at the top of a platinum crucible. They are heated at 150°C/h until 1500°C and remain for 4 hours at this temperature. This cycle is repeated twice. Volume increase of the sample and glassy phase found on the crucible give the total exuded volume.
- Louisville test: samples are pellets of 36-mm diameter and 5-mm high, taken at 4 reproducible positions. Volume increase is measured after 16 hours at 1500°C.
These tests have been performed on AZS blocks of varying colors. With both tests, we can see a strong correlation between color and exudation rate as described in Fig 5 when we plot exudation level in L*, C* space.
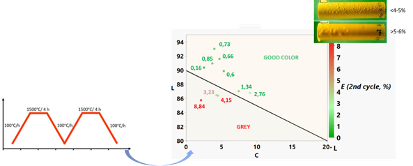
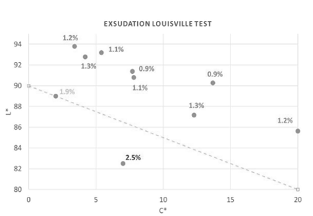
Exudation rate could be 2 to 4 times higher on a grey block. This exudation can weaken the refractory by increasing its porosity and therefore its corrosion speed. It can also trigger glass pollution with cords, knots, or secondary Zirconia crystals as highlighted in Fig 6.
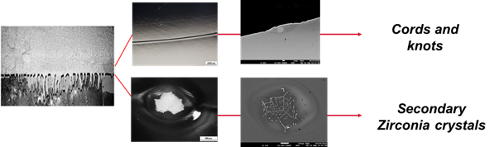
Thus, oxidation control has a major impact on glass quality and furnace performance.
Importance of reliable control and specification
To guarantee a long-lasting furnace with the best yield possible, SEFPRO has added a specification – based on exudation and blistering tests – for AZS blocks in order to select only blocks with the ideal color, meaning the optimal oxidation state. A good block will have a color following the equation:
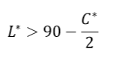
This value is measured on the sawn top face, at 4 different positions, as statistical controls proved that this number of controls is satisfactory for a meaningful value. Control points are described in Fig 7.
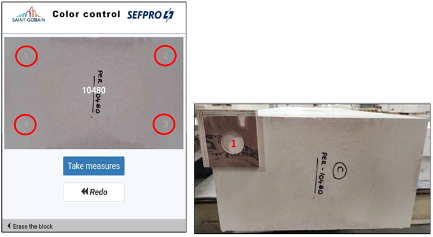
This new color specification is now fully integrated into the set of standard specifications for all sidewalls, throat blocks, and submerged walls that allow color measurement on a clean sawing face.
In part 2, to be printed in the next issue of Glass 5.0, SEFPRO discusses Consequences of shrinkage cavity and filling optimization, Surface quality – Upcoming improvements, Use of image analysis for reproducible measurements and Data collection and new product development.
Add a Comment