Cullet – Another Step Towards Glass Sustainability
By Chris J. Hoyle, Senior VP, Technical Director
Kevin L. Fulkerson, VP of Technology
Brian J. Naveken, New Project and Business Development
Introduction
There has been much written and said about glass being infinitely recyclable and yet, in the USA, the national container-recycling rate is less than 40%. Some European countries have container recycling rates in excess of 90%, clearly, the USA could do better. In order to improve the situation, the USA has to recognize the benefits that recycled glass brings to the manufacturer and to society as a whole. This article will focus on the benefits and risks of increasing the use of recycled glass in manufacturing. The benefits include higher energy efficiency, lower carbon dioxide emissions, longer furnace life and increased capital efficiency. The risks include increased defect levels, contamination and off-target composition and properties.
Recycled glass or cullet is a batch ingredient that is often not given the attention it deserves, but as the fraction in the batch mix increases, the impact on the final product also increases. As with any raw material the cullet should be of consistent and repeatable quality, there is much truth in the old adage “garbage in, garbage out.”
Sources of Cullet
There are three sources of cullet available to most manufacturers, the plant’s internal cullet, cullet from a downstream processing plant and post-consumer recycled cullet. Internal cullet results from rejects and/or manufacturing scrap within the melting, forming and annealing process and, depending on yield, it can provide 10 to 20% of the daily pull. Internal cullet is an exact match for the chemistry and redox and does not require any adjustments to the batch recipe. The same is true for cullet from downstream processes, but this is usually a small fraction of daily pull. Together these two sources amount to 15 to 25% of daily pull. Increasing use above these levels requires external sources involving some kind of post-consumer recycling.
It is unlikely that the chemistry and redox of external cullet will match that of the glass being produced and therefore adjustments to the batch recipe are required. The glass manufacturer is looking for a supply with repeatable and consistent physical and chemical properties and these should be checked at least as often as the other raw materials. Recycled cullet can contain glasses of different compositions and the onus on the cullet supplier is to deliver a consistent product. The sorting techniques used by the cullet supplier aims at delivering a high quality, consistent product, that the manufacturer can rely on.
No matter what the source, cullet should be stored and handled with the same care as the other raw materials to prevent degradation by size reduction, contamination or weathering. Cullet can bring positive benefits and the quality should not be compromised.
Batch Chemistry
The glass industry refers to glass furnaces as melters but they are chemical reactors. The transformation of raw batch to glass is a complex physical and chemical process. Silica, the major component of most commercial glasses, has a melting point of 1713°C (3115°F), a temperature well above that found in the majority of furnaces. Clearly something other than melting is occurring. Soda ash (sodium carbonate) starts to melt and decompose at about 800°C (1472°F), forming carbon dioxide gas and sodium oxide liquid. The sodium oxide liquid surrounds each sand grain and reacts with the silica at the surface forming sodium silicate. The calcium and magnesium carbonates also melt and decompose, giving off more carbon dioxide, the resulting oxides reacting with the sodium silicate to form soda-lime-silica (SLS) glass. These chemical reactions require time for the reacting species to diffuse through the boundary layer, react and then diffuse away again with energy, as these reactions are endothermic. The amount of energy absorbed by these glass-forming reactions is 490 kJ/kg or 116 kcal/kg.
Cullet is already glass and no chemical reactions occur. The cullet simply heats up, softens and becomes liquid. There is no phase change from solid to liquid, as glass is a “super-cooled” liquid and therefore no latent melting energy. As stated earlier, the conversion of batch to glass begins with the decomposition and melting of the carbonates evolving into carbon dioxide. For every tonne of glass produced from SLS batch, approximately 175 kg of carbon dioxide is given off absorbing 0.16 GJ/tonne or 38.2 kcal/kg of energy, as it is heated to the furnace exhaust temperature.
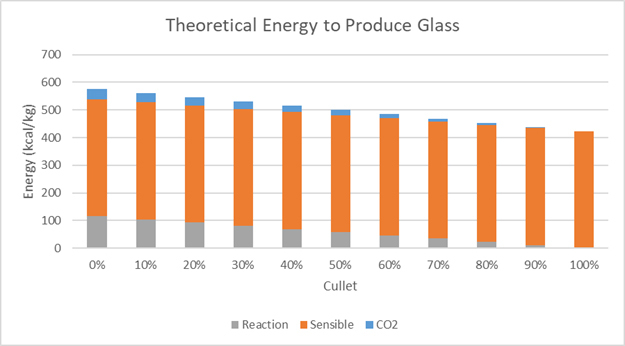
Figure 1: Theoretical energy to produce glass consist of sensible energy to heat glass, reaction energy and sensible energy to heat carbon dioxide gas. The energy required reduces as the amount of cullet in batch increases.
The amount of energy required to produce glass at 1500°C (2732°F) comprises three components, the glass forming reactions, the energy to heat the carbon dioxide and the sensible energy to heat glass to the production temperature, as shown in Figure 1. Producing glass from cullet requires 27% less energy than from batch, a significant reduction.
The reduction in carbon dioxide emissions by increased use of cullet will be a major component in the drive to lower the carbon footprint of glass melting. The introduction of carbon cap and trade systems will add economic incentives to that derived from lower specific energy consumption. In the drive to ecofriendly sustainable glass production, reliable sources of post consumer cullet will be increasingly important.
Batch Physics
The addition of cullet to the batch mix introduces changes to the physical properties that influence the size and thermal behavior of the batch piles in the furnace. The two key properties are density and thermal conductivity and this paper shall look at them in turn.
The density of batch with no cullet is about 1300 kg/m3, that of cullet is about 2500 kg/m3 and, as the fraction of cullet increases in the mixture, its density increases non-linearly, as shown in Figure 2.
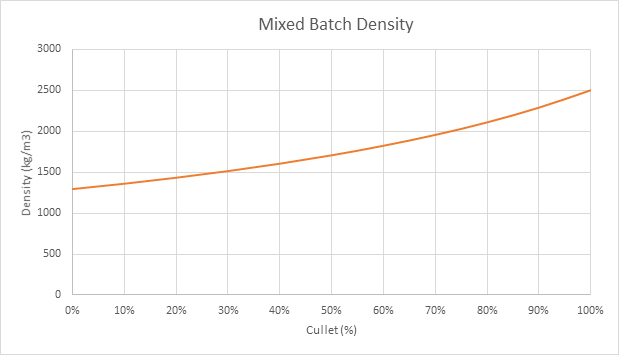
Figure 2: Mixed Batch Density - More cullet the higher the density.
The higher the density the lower the volume occupied for the same mass of batch charged. Thus, if the batch covered area in the furnace remains the same, the height of the piles will be lower reducing the distance from the surface to its center and speeding up the rate of heating. If the overall batch length remains constant this implies that superstructure temperatures can be reduced. However, this may be mitigated by the fining temperature needed to maintain glass quality.
At temperatures below 1100°C (2012°F) cullet has a higher thermal conductivity than batch, as shown in Figure 3. Until the batch heats up to temperatures over 800°C (1472°F), when the first liquids appear, the difference increases, above this temperature the difference decreases, with batch finally catching up at 1100°C (2012°F). Assuming the cullet and batch are intimately mixed, the higher thermal conductivity significantly increases the conduction of heat through the batch piles. This will also reduce the time taken for the pile to melt out, again, implying that superstructure temperatures can be reduced to maintain the same batch length.
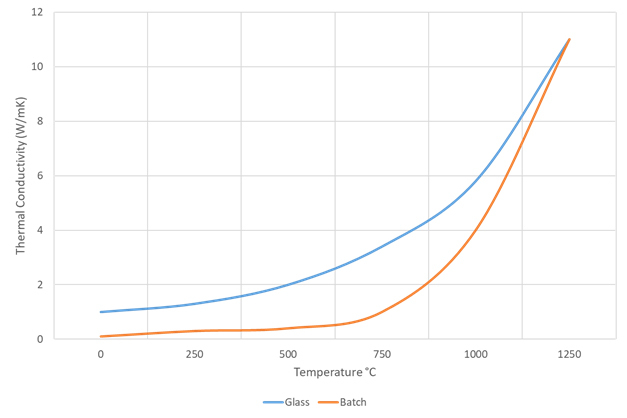
Figure 3: Batch Thermal Conductivity - No cullet compared to cullet.
Model Study
To investigate and quantify the effect of batch to cullet ratios, a Computational Fluid Dynamics model study was undertaken. The furnace modeled was an electrically boosted oxy-gas tank melting a typical flint SLS container glass. In the study, the furnace design, boost and pull were kept constant and a series of models run with the cullet varying from 0 to 100% in 20% increments. To keep the glass quality constant throughout the series of models, the target throat temperature was maintained within 1°C by adjusting the fuel flow.
The results of the study confirmed the trends predicted from the theoretical analysis. The glass quality indices and average bulk glass temperatures were constant throughout the series of models. Energy consumption fell by 35%, as cullet increased from 0 to 100% (Figure 4). The energy reduction falls in line with that predicted from theory taking into account the thermodynamic efficiency of the furnace modelled. Practically, this level of percentage reduction will be seen on any type or age of furnace, as it results from a change in the theoretical energy and is independent of furnace design and operation.
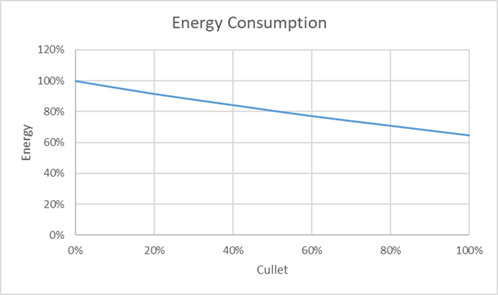
Figure 4: Energy Consumption - Reduces with the use of Cullet.
The average combustion space temperatures in the models fell by 38°C (68°F), as a result of the lower fuel flows. This temperature decrease will directly reduce refractory corrosion and the lower firing intensity will reduce carryover and its consequent corrosion of the superstructure refractories. On regenerative furnaces there will be less blockage and plugging of checker packs, requiring less frequent checker burn outs. Reduced corrosion and carryover will result in less maintenance and lower defect levels from refractory inclusions. In addition, the lower temperatures and firing intensity have a positive effect on NOx, with a reduction of over 60% as cullet increases from 0% to 100%. This energy reduction means there is less work for the emissions control system and the consequent reduction in reagent use.
As a result of the Paris Agreement, economic incentives to reduce carbon emissions are being implemented. The most common of these incentives are cap and trade systems, where the carbon emission is capped, the cap reducing over time and a marketplace established where carbon emissions can be traded. The use of increased proportions of cullet provides an excellent means of reducing carbon dioxide emissions. The reduction comes from both the elimination of carbonates in the batch and the improvement in energy efficiency, as shown in Figure 5. The total mass emission falls from 0.333 kg/kg of glass melted to 0.07 kg/kg, a 79% reduction. The reduction, due to the elimination of the carbonates, is fixed by the batch chemistry. While reduction, due to improved energy efficiency, depends on the type, age and efficiency of the furnace.
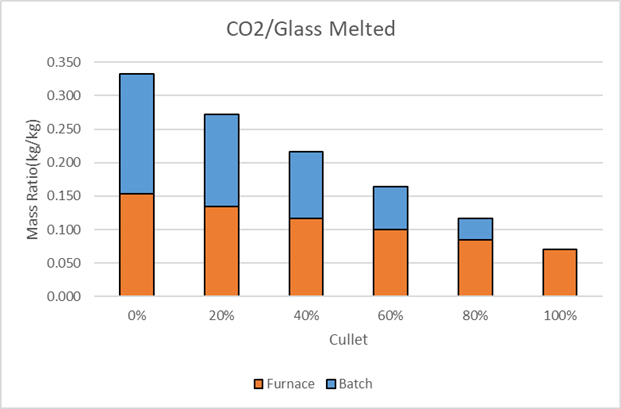
Figure 5: CO2 Production Decreases with the use of Cullet, Lowering its Carbon Footprint
Cullet
As stated, there are three sources of cullet available to the glass manufacturer. The two most reliable sources being internal and that from a downstream processor. The third source, post consumer cullet, is the least reliable but one that will become necessary, if increased cullet use is to be realized. Manufacturers want all their raw materials to be consistant from day-to-day, week-to-week, for the production of consistant quality wares. Glass quality in terms of chemistry and physical properties need to be repeatable.
Post consumer cullet is no exception to this rule and, therefore, it is incumbant on the cullet suppliers to deliver a chemically and physically consistent product. Cullet recycling has become a sophistocated industry capable of providing clean cullet, sorting it by color, chemistry and size to maximize the value and use to the glass manufacturer.
Conclusions
Cullet is an important raw material that will help the glass industry achieve sustainability. The use of cullet improves energy efficiency, reduces carbon dioxide and NOx emissions, reduces wear and tear on furnaces, reduces the amount of waste going to landfills, and reduces the need to produce raw materials. Quantifying these savings will depend on local circumstances for each plant. The decision to increase post consumer cullet use will be based on the local availability of good quality cullet and the economic and social benefits. Improving cullet recycling systems should become a focal point for manufacturers, furnace designers and cullet processors, to ensure the long term survival and sustainability of the glass industry.
Add a Comment