Pursuit of Technology Balance
A Three Part Series of Melting Characteristics – Part 2
Replace Throats with Waists
By: Roberto Cabrera, Vice President of Technology and Engineering – Vitro
Editor’s note: Roberto brings over 37 years’ experience to the glass industry and is currently responsible for engineering and capital projects for the Vitro architectural glass business in Mexico and the USA. Roberto is also a BTU Award recipient and sits on the Glass Manufacturing Industrial Council Board of Trustees.
Introduction
With non-float glass furnaces trending towards higher glass pulls and longer campaign life, a throated style glass exit is not the ideal choice. When it comes to furnace life, throats have traditionally been the weak link, resulting in quality issues and lower campaign life than fuel-fired furnaces. Fortunately, an alternative solution readily available from the float glass industry exists and is easily adaptable. This solution, known as a "waist," is employed in all float glass plants.
Glass Furnace Throats
The function of a furnace throat is to effectively extract molten, refined glass from the furnace towards the front end. For more than a century, throats have been utilized alongside deep refiners, weir walls, and refining shelves, as well as with technologically advanced flat-bottom furnaces that have advanced beyond these outdated features.
The main wear mechanisms of a throat are:
- Temperature
- Glass chemistry
- Pull rate or glass velocity
In throated furnaces, throat wear (refractory dissolution rate) is dependent upon temperature (exponential) and glass flow rate.
What is a Straight-Through Furnace Throat?
A straight-through throat (Figure 1) is a rectangular opening that is flush with the furnace or melter bottom. Therefore, the throat entrance temperature is the same as the bottom temperature at this location. This style of throat is used in furnaces with glass types that have lower thermal properties which results in lower bottom temperatures.
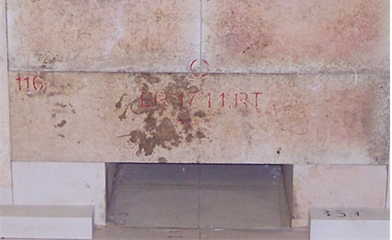
Figure 1: Example of a straight through throat
What is a Sunken Furnace Throat?
A sunken throat (Figure 2) is very similar to a straight-through throat with the exception that it is not level or even with the furnace bottom. Sunken throats have advantages over straight-through throats. These are:
- Inhibits return flow, saving energy
- Lowers throat entry temperature reducing corrosion
- Increased distance from glass surface to throat entry decreases shortest path particle residence time
- Electric boost addition for low pull operation and hot hold
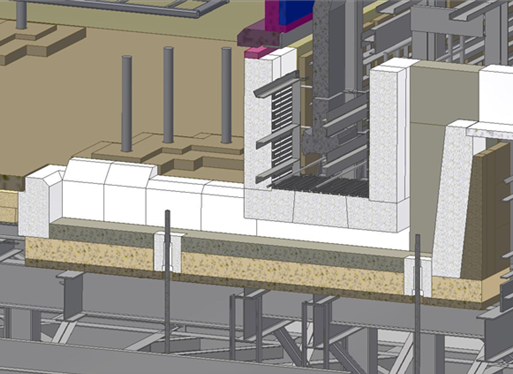
Figure 2: Example of a sunken throat
Both types of throats undergo wear over time, leading to changes in dimensions and flow characteristics, as depicted in Figure 3. The lifespan of a throat varies dependent on furnace type, throat design, pull and glass composition. Some cases throats can last as little as 3 years and Toledo Engineering, for instance, experienced a throat lasting over 16.5 years without causing a shutdown of the furnace.
The temperature at the entrance of the throat significantly impacts downstream temperatures and ultimately influences glass quality. Beyond the throat lies the riser, which, although not extensively covered in this article, warrants mention due to its diverse range of shapes, sizes, and designs.
Now, is there a technological solution for replacing throats? Absolutely. This solution offers the advantages of extended operational campaigns and reduced wear, all while incurring minimal energy penalties.
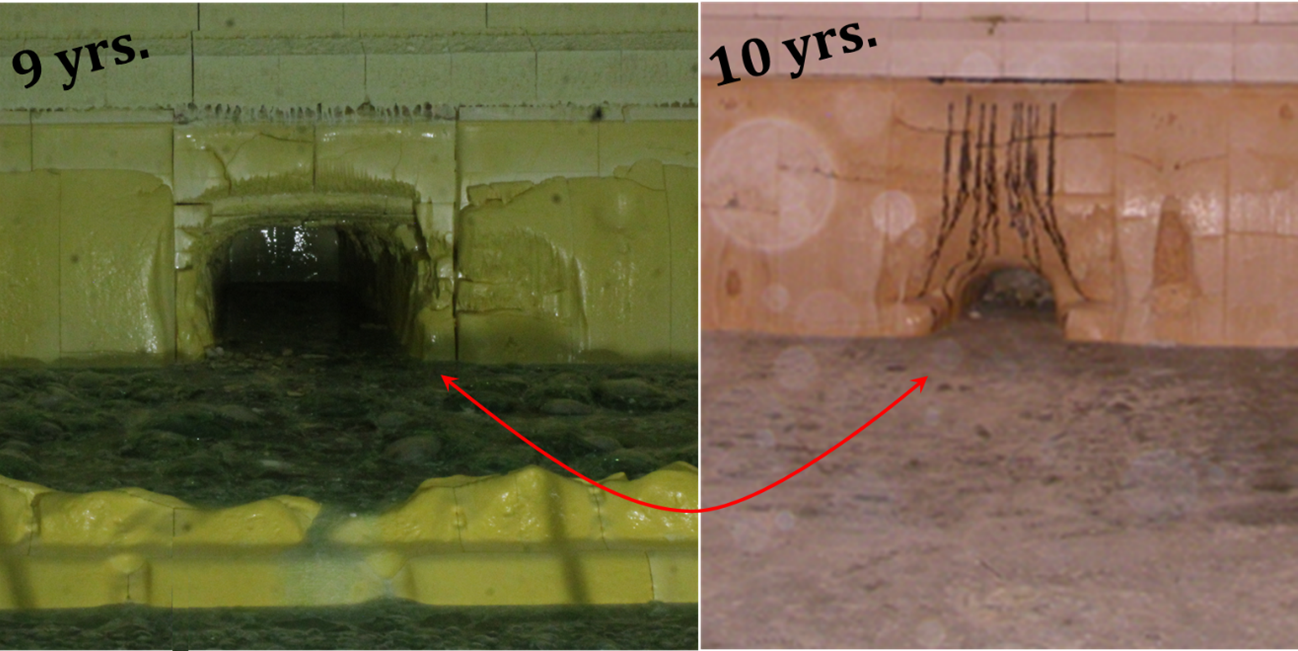
Figure 3: Straight-through vs. sunken throat wear comparison
Glass Furnace Waists
A glass furnace waist is a canal that connects a melter and more often the refiner to a working end, canal or a distributor. Figure 4 is an example of a waist connecting to a distributor feeding rolled glass forehearths. Waists serve as essential components utilized in all float glass plants, demonstrating their universal effectiveness since the 1970s. Waist coolers (Figures 5 & 6) are used in conjunction with a waist in order to regulate glass flows from the refiner to the working end. Adjustment is accomplished using different depth coolers for different immersions.
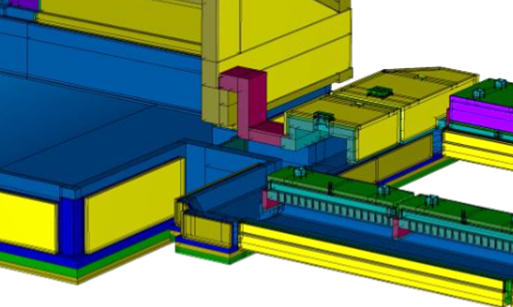
Figure 4: Waist connecting refiner to forehearth distributors
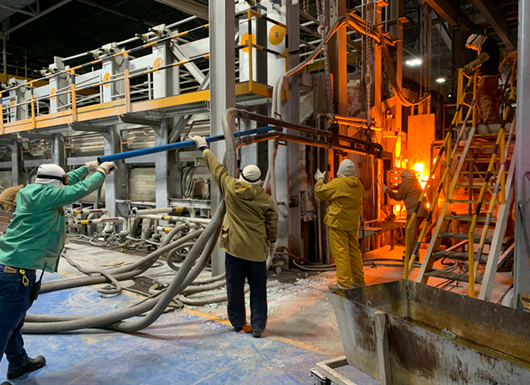
Figure 5: Waist cooler installation
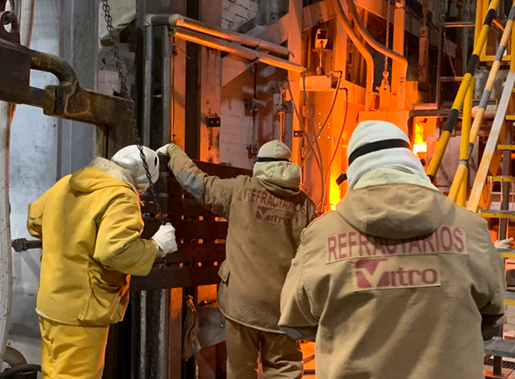
Figure 5a: Waist cooler installation
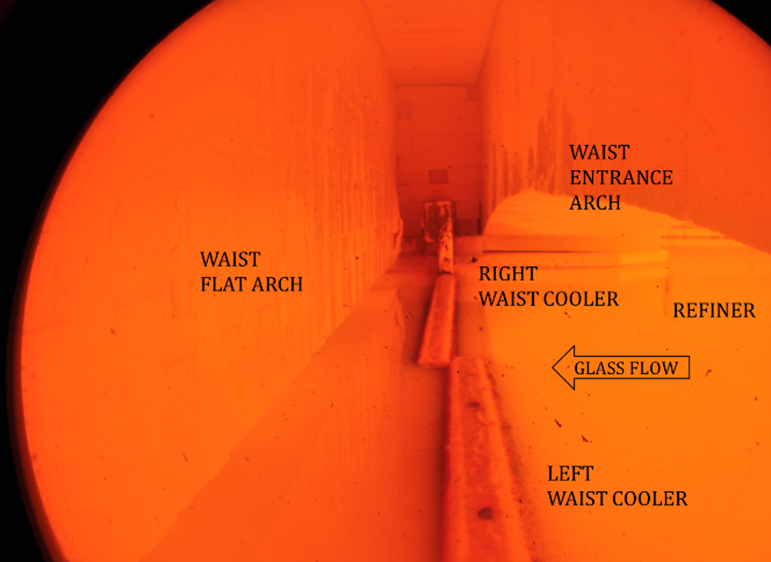
Figure 6: Waist coolers
Waist vs. Throat Risk Assessment
Pros
- Ideally suited for larger furnaces with pulls over 250 mtpd
- Quality improvements due to less refractory wear
- Extended campaign life – TECO float furnaces have campaigns up to 22 years and the waist is not the reason for the end of campaign
- Production proven and standard on float furnaces
- Eliminates risers
- No need for a throat heating system
- Heat-up ease
- Can’t freeze a waist!
Cons
- Not ideally suited for all electric furnaces or end-port furnaces (at this time)
- Operations personnel not experienced with waists
- Opposing personal views
- Risk mitigation
- Not proven with weir walls
- Cannot use with a deep refiner
Water System is Critical for Waist Coolers
Water cooling system engineered to provide enough flow to maintain water temperature
- Stainless steel metallic hoses
- Closed circuit with low make up amount
- Continuous flow at temperature below boiling point – preferable around 45-55°C
- High purity water quality – low conductivity to avoid piping clogging from hardness
- High initial capital costs
- Continuous maintenance to keep high purity water
- Requires back up systems and redundancy to prevent failures
Failure of this system will provoke a major issue, such as melting of steel inside the furnace with bubble formation from dissolution of steel, downward drilling of bottom refractory and exploding coolers just to name a few.
Conclusion
Like the Merkle suspended backwalls discussed in the first part of this article series, waists represent a technological advancement over throats in furnaces, contributing to the overall technological balance. This is particularly evident in larger oxy-fuel and cross-fired regenerative furnaces, and with appropriate design and engineering, in all-electric melters. Float furnace experts have been aware of the benefits of waists for years, prompting one to consider asking them if they would ever consider exchanging their waist for a throat.
Add a Comment