Furnaces for Low Iron Solar Glass
Low iron glasses for solar PV (photovoltaic) applications are generally characterized by the following physical and chemical properties:
- The total iron content is less than 200 ppm;
- The glass redox (Fe 2+/Fetotal) is less than 10%;
- Seeds (very small bubbles) target is less than 15/kg;
- Light transmission is greater than 90%.
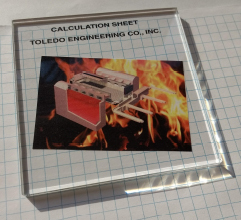
To achieve these glass properties requires a furnace that gives the operator good control of the energy profile and flame oxidation state along its length. There are two principal designs of air/fuel furnaces employed by the majority of the world’s glassmakers, end fired and cross fired. Both types of furnace are well proven, but for the large scale, high pull production of high-quality glass, the cross fired furnace design (Figure 2) is the superior choice. TECO has provided these very successful, production proven designs not only for rolled glass, but also for both container, and of course, float glass.
End Fired vs. Cross Fired Furnaces
- Currently in operations, the largest operating end port furnaces, all TECO designed, are about 155 m2 producing about 500 MTD for container quality glass. The pull rate and residence times for low iron solar glasses would require at least 250 m2 or more, an increase of more than 60% over current proven end port technology. Meanwhile, cross fired furnaces over 600 m2 are well established in operation.
- Theoretically, aspect ratios of end fired furnaces have a maximum of 2:1 (length: width), due to limitations of flame coverage, whereas cross fired furnaces have no such limitation. The higher aspect ratio of cross fired furnaces allows the development of distinct melting and fining zones, improving glass quality despite the challenges caused by the oxidized fining system, commented upon above.
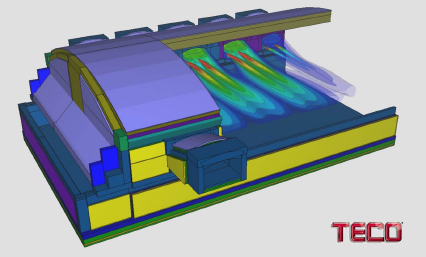
- For end fired furnaces, the heat release over the length of the furnace is largely fixed by the port and burner design, making it very difficult operationally to vary the energy and oxidation state, if required, to control the convective glass flows. Cross fired furnaces, especially with compartmented regenerator chambers, allow control of both energy profile and oxidation state along their length. On larger, higher output furnaces, the width for the end ports (Figure 3) is less additive than the length for the side ports. Finally, our customers have achieved 0.007 Fe2O3 levels in their glass, providing a distinct, measurable advantage in the market.
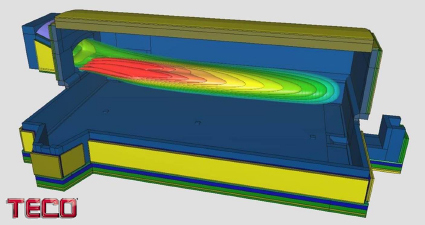
- The control of the batch charging pattern is very important for the production of high-quality glasses. End fired furnaces of this size will have two oscillating chargers, one each side, producing circular piles of batch that do not provide full batch coverage. The doghouse corners are a high and risky wear point, which due to glass color cannot be chrome refractory. Cross fired furnaces of this size have a full width doghouse, with no corners to wear, and employ blanket chargers producing batch logs covering the entire width of the melting zone (Figure 4), resulting in very efficient radiant heat transfer and melting, due to the well-controlled, optimized surface area of the batch logs.
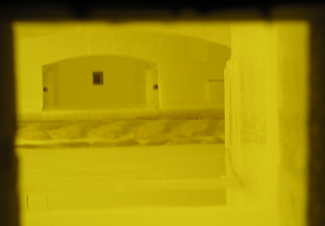
- Some end port designs include weir walls (outdated technology) to impose a refining zone, whereas in a cross fired furnace this zone can be effectively controlled by the energy profile and waist cooler depth. Of course, weir walls wear away after only a few years and therefore their impact on the glass flow is constantly changing. This affects operational stability until they wear away completely. This worn AZS refractory causes defects, ream and cord, introduced into the final product, which directly reduces plant pack yield and profitability. Further, as CFD modeling and industry comments reveal, once the weir wall is dissolved away, the furnace energy and glass quality is negatively impacted.
- The throat is a high wear area and will require overcoating to achieve a reasonable life, maybe more than once in a 10-year campaign. Attempts to reduce the wear by having two throats have been made, but TECO has reservations about this approach. Fused cast refractory wear is proportional to the exponent of the temperature and the square root of glass velocity. Thus, the impact of throat entry temperatures in excess of 1400°C far outweighs any reduction due to the lower velocity resulting from using two throats. It is known from real world physical tracer studies, and confirmed by (Computational Fluid Dynamics (CFD) mathematical modeling, that furnaces are very ‘handed’, meaning any batch introduced on the left hand or side melts to form glass that stays on the left side, and vice versa. Having two throats means these flows will stay separated and could result in different glass qualities between the two sides.
- The cross fired design also eliminates the throat weak link by incorporating unique designs based on TECO long-life furnaces. These technologies are widely employed in float glass for the production of very high-quality glass, and adapted in many of our other furnace designs. This allows control of the flow of glass to and from the refining zone, thereby achieving both higher quality and longer furnace life, while allowing the operator greater flexibility.
- Cross fired designs exhibit very long campaigns due to the elimination of several refractory high wear features and incorporating improved access for maintenance. TECO has many documented furnace campaigns reaching in excess of 20 years, and even with low iron glass, a furnace with good operation and maintenance practices can have a life approaching 15 years.
- End port furnaces are in general more energy efficient than a cross fired furnace of the same size (same dimensional m2), but only in that single parameter. The cross fired furnace will produce better quality, higher yields and longer campaigns, resulting in much lower total cost of ownership to the glass producer. This is correlated in TECO furnaces for container production, where a cross fired furnace has achieved production at 800 MTD pull, but our largest operating end port furnaces produce 500 MTD of container ware (Figure 5).
In summary, for high output, high quality low-iron glass production, the optimized choice for meeting the low Fe2+/Fe3+ ratios required for high energy transmission for solar PV applications can only be achieved economically by utilizing a cross fired furnace design. There are many more nuances to low-iron furnace design necessary to achieve high quality and long life, but the first design step is certainly the choice of a TECO cross fired furnace. To learn more about TECO’s capabilities, contact our Technical Sales team at sales@teco.com or call (011) 419-537-9711.

Add a Comment