Proper Cullet Handling
Another Key to Sustainability
By Brian J. Naveken, Project and Business Development
The TECO Group continues to be a standard bearer in the development, construction, and implementation of highly sustainable glass plants and glass manufacturing processes. In previous batch house articles, we have emphasized that when your plant is producing high quality mixed batch, the outcome is better quality glass for the downstream production process which, in turn, results in optimal plant performance and maximum profitability. It is reasonable to deduce that high quality glass will help to minimize cullet generation. However, some cullet always results from the manufacturing process regardless of the level of efficiency, therefore it is important to consider the methods used for processing and effectively handling cullet, in order to minimize operating costs, optimize particle size and minimize fines.
Two primary trends have emerged in the glass industry regarding the use and handling of cullet. First is the significant increase in the use of foreign cullet (i.e. bought in cullet), which reduces raw material and melting costs, while lessening refractory erosion and decreasing furnace emissions. Second, the automated handling of cullet has become prevalent, thus reducing manpower and curtailing personnel safety risk.
The Cullet Cycle
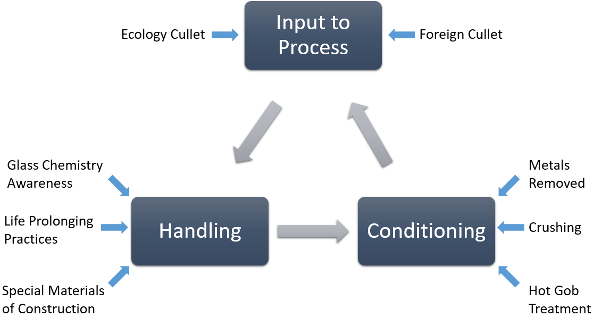
Possessing a precise and detailed understanding of the cullet cycle is of paramount importance as we examine the key to higher sustainability in batch plants and cullet handling systems. As shown in Figure 1, cullet processing considerations are intricately interrelated. In many circumstances the material is generated from defective and broken products from the glass plant. However, cullet from recycling operations or foreign cullet plants now form significant proportions of the container glass and glass fiber batch compositions. While there are some benefits to using more cullet in glassmaking operations, environmental concerns and energy reduction costs are the major elements that are driving the move toward the use of more outside cullet.
Cullet Handling
Once produced, the cullet moves via conveyors, bucket elevators, diverters, chutes and other equipment specifically designed to handle this material. However, this equipment is subject to severe abrasive attack due to the relative hardness of glass and the sharp edges of cullet. An experienced contractor and knowledgeable engineering team can make a significant difference by implementing numerous techniques that minimize or eliminate wear on chutes, elbows, deflector plates and other material contact points.
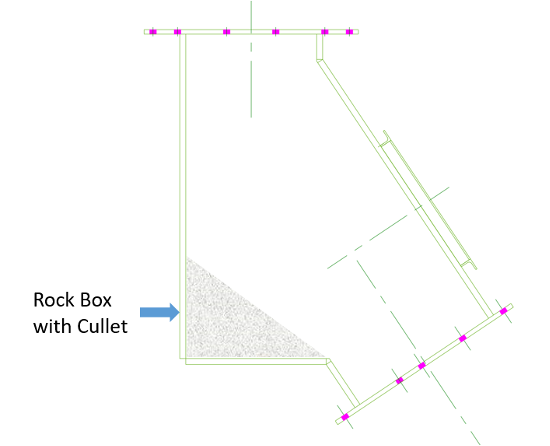
For example, rock-box construction, as shown in Figure 2, is commonly used at the elbows of chutes to prevent wear, thus extending life at minimal cost. With this technique, the cullet itself is utilized as the wear-resistant material.
Another method, the use of abrasion-resistant (AR) alloys, adds initial cost to the project, but saves maintenance repair hours, and ultimately decreases the total life cycle cost. Hoppers, or sections of hoppers and chutes, benefit from using AR materials for basic construction or as liners. Figure 3 shows a chute constructed with AR steel plating. AR steel is available in hardness ratings ranging from 240 all the way up to 700 Brinell, with higher Brinell hardness resulting in longer life for the steel. The choice of hardness depends on the type of abrasion, sliding or impact, the apparatus will experience, and the cullet throughput. Alloys with chromium carbide, exhibiting Vickers hardness ratings as high as 1200, are a good choice for hoppers and chute overlays for high quality glass production. Contamination has proven to be a non-issue.
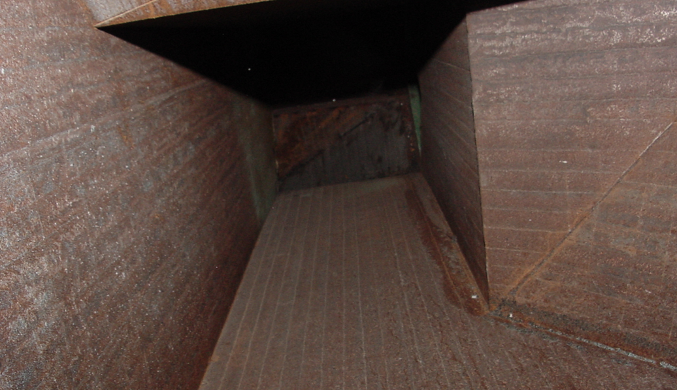
Another option is the use of ceramic materials, which can be utilized as liners in bins, hoppers or chutes. While they may be too brittle for use in some applications, ceramics make for excellent sliding surfaces because of their hardness and low coefficient of friction. Additionally, they are suitable for impact erosion, provided the proper thickness is selected and the material is installed rigidly.
Another method to be considered involves the use of various rubber-like elastomers as liner material to accommodate impact abrasion. These materials, however, are not particularly suitable as a sliding surface, due to high coefficients of friction, and can be cut by the cullet, resulting in the imbedding of cullet in the rubber.
It is important to keep in mind not all alloys are suitable for use at certain wear points. For example, stainless steel can cause nickel-sulfide stones, while abraded iron and chrome can also create problems if they excessively contaminate the glass. Ultimately, the batch plant contractor must possess extensive knowledge of glassmaking chemistry to avoid selecting improper materials and application designs.
Hot Cullet Conditioning
The term ‘conditioning’ refers to the refining of the cullet for subsequent handling and processing. As an example, during container glass cullet conditioning, the hot gobs produced amid a job change are discharged into a water-filled quench tub, with a drag-chain conveyor feeding a conveyor or portable hopper. In the case of small gob conditioning, the temperature gradient is steep enough to fracture them once they hit the quench tub water. A water bath with a screw is often used for smaller containers, and a wet oscillating conveyor for E-glass.
In the case of large gob conditioning, the size and shape make it difficult to build up a sufficient temperature gradient within it to fracture the gob when it comes in contact with the quench tub water. These large gobs remain hot and tend to agglomerate in the quench tub. It is common practice to install a ‘mangler’ that flattens the gob and gives the resultant ’patty’ a sufficient temperature gradient to fracture into more manageable sized cullet when it hits the quench tub water.
Crushing
The next step in handling cullet efficiently is the cullet crushing process. Several types of cullet crushing equipment are available. Choosing the suitable apparatus and machinery for any given facility depends on the specifications, budget and other pertinent factors of the project.
The jaw crusher is a dependable and long-lasting piece of equipment that has been used throughout the glass industry for many years. It works best when choke fed (inlet always full), which allows the cullet to primarily wear upon itself, thus minimizing the potential for large pieces of cullet to slide through the jaw plates and into the process. Operators, however, should be aware that jaw crushers do generate cullet fines that can tend to become a material handling problem, personnel hazard and become airborne in the furnace, which can result in glass wetting of the superstructure. The fines can similarly become a carry-over component into the regenerators.
Roll crushers have also been used in glassmaking for many years with excellent results. They are relatively economical and best suited for controlling particle size. Roll spacing and roll speed are adjustable and a primary and secondary set of rolls can be used to accommodate various sizes of cullet, allowing the crusher to be specifically designed to provide optimum particle size. Roll crushers produce minimal fines and rarely yield oversize particles.
Finally, high-speed impact crushers are also an option in the cullet crushing process. However, additional and somewhat unique factors must be taken into account when considering their use. Most high-speed impact crushers are based on a rotary drum with abrasion-resistant breaker bars, sometimes referred to as hammers. Due to the high velocity of the rotary breakers, and the sharpness of the cullet, these crushers typically see the highest degree of abrasion and require the greatest amount of maintenance. They are best suited for applications in which smaller cullet particle sizes are required, where the cullet mesh size is to match other batch materials, or where it is essential to separate cullet from foreign materials such as metal.
Metal Removal
Because the cullet supply can provide an excellent path for tramp metals to enter the glass batch, another important step in the conditioning of cullet for reuse is to magnetically separate unwanted ferrous tramp metals. Numerous ferrous metal extraction schemes can be considered for this part of the process, such as the magnetic head pulley method, the grid and plate magnetic method, and the overhead and cross-conveyor magnet method. It is also important to remember that some metal removal applications require removal of the non-ferrous tramp metals, which is accomplished with a separate non-ferrous detector and contaminated material removal system.
Float Glass Conditioning
With all of these considerations on the table, TECO has also been involved in developing and advancing special cullet processing applications. For example, float glass conditioning differs from basic glass conditioning, as seen in Figure 4.
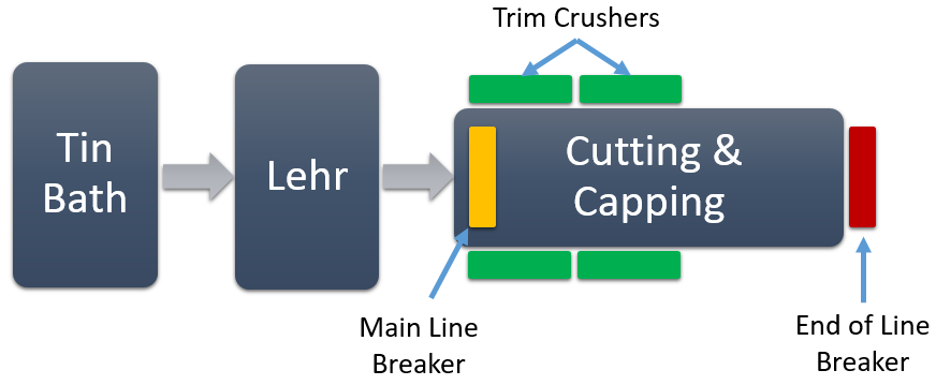
Defective float glass can only be rejected after the molten glass passes through the tin bath and the formed sheet of glass exits the lehr. In the case of an emergency, or when the ribbon is defective, the ribbon is crushed by rotating hammer type breakers at the beginning or end of the cold end, as seen in Figure 5.
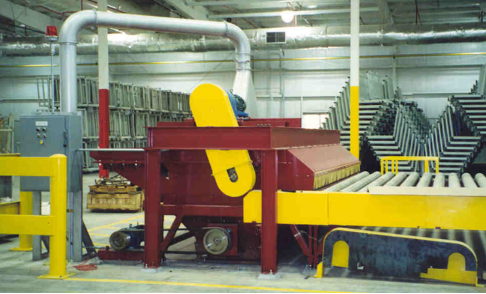
Choppers, Figure 6, are used below the process floor to handle the cullet generated during breaking or trimming and produce cullet between 645 mm2 and 1300 mm2. The cullet is conveyed back to the batch plant where it can be crushed and further reduced in size if necessary and transported directly to the cullet silo. Float glass conditioning offers capabilities that streamline the cullet handling process and results in sustainability that is key to the long life of the plant.
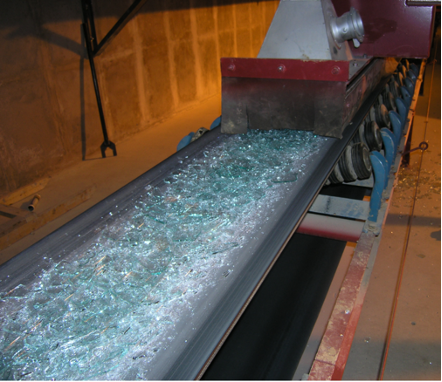
Summary
In summation, payback on cullet system improvements depends on each plant’s circumstances, but evidence throughout the years has continued to show that cullet system upgrades are a good investment. The ultimate goal in most plant operations is to scale back human intervention and minimize equipment maintenance while optimizing automation in batch plant and cullet material handling systems. With modern advancements in technology and improved processes, this can be accomplished to a greater degree than ever before. The TECO Group has developed and implemented these necessary tools and techniques, and when it comes to cullet handling, we have the expertise, experience and know-how to help our clients achieve optimal plant performance and maximum profitability.
Add a Comment