Maintaining schedule on a greenfield glass plant despite Covid-19
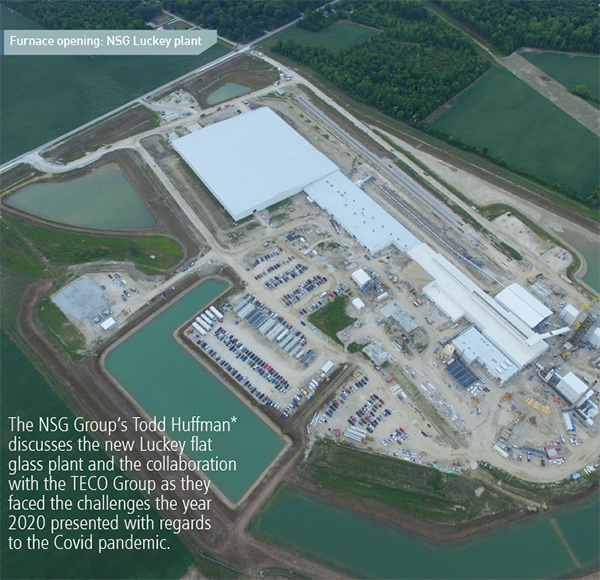
The NSG Group is in the final stages of completing a turnkey float plant in Luckey, Ohio. Construction began in the second quarter of 2019 and production will start at the end of 2020. The $265 million, 511,000ft2 facility, will melt 600 tons per-day of transparent conductive oxide (TCO) coated glass to supply the rising solar marketplace, as companies and communities strive for carbon emission neutrality. To accomplish this endeavour, the TECO Group was chosen as the design-build general contractor.
What was the motivation for building a turnkey greenfield glass plant in the USA?
Market demand for TCO glass. The global production of TCO glass is expected to accelerate, and this represents our commitment to our customers to supply value-added products to support the use of renewable, sustainable energy.
Why and how was the Luckey, OH site chosen?
First Solar, the only US-headquartered company among the world’s 10 largest photovoltaic manufacturers, operates the western hemisphere’s biggest solar manufacturing footprint in Perrysburg, OH and NSG has a long-term supply agreement with it. Proximity to a skilled labour force, existing operations, raw materials, transport, and utilities were all factors the company considered. I should mention here, that the TECO Group was an active participant in determining the exact location. Their involvement on this project started with the site selection.
What were some of the unique challenges in regards to Covid-19?
The two biggest challenges regarding Covid-19 were ensuring the health and safety of everyone on site as well as maintaining schedule.
What effects did Covid-19 have on the project?
Three effects come to mind. The first of these is the reality of contact tracing. At one point, we experienced several symptomatic cases, which forced about a third of the work force off-site for two to three weeks. These cases were not spread across the entire workforce but generally within a specific trade discipline. The second challenge being faced is international travel. Gaining entry and exit for global technical experts, necessary for the final steps of installation and commissioning of equipment, has proven to be quite the challenge. Lastly, some key componentry for the project coming from overseas has been delayed either in the country of manufacture or in port.
How was NSG and TECO able to stay on schedule?
This has been a challenge but the collaboration and quality of teamwork between NSG, TECO, Dreicor, sub-contractors, the State of Ohio and the local community has kept the project timing very close to plan. One of the things TECO did to minimise schedule impact was to backfill selected areas from the TECO offices.
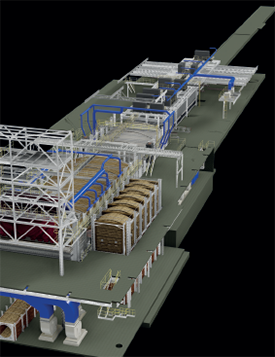
Based on multiple industry accounts, other firms around the world have had to suspend construction and send personnel home. How was this plant construction able to continue?
Within the State of Ohio, construction firms were granted an exemption to the extent they were operating in support of essential businesses. Ohio identified glass manufacture as an essential business. NSG and TECO’s pro-active planning measures to ensure everyone’s health and safety were key.
What measures were implemented to insure peoples’ safety throughout Covid-19?
TECO and Dreicor, in conjunction with NSG, designed a Pandemic Response Plan for the jobsite. In the early stages, before the project experienced any cases, the NSG/TECO team were having meetings dedicated to formulating and coordinating an execution strategy to efficiently respond to COVID-19 cases discovered during the project. Throughout this process, there has been high-level management involvement from both companies and excellent collaboration among all the team members to address workforce safety. This plan was based on State of Ohio and CDC guidelines and a risk assessment to better fit this specific jobsite. One example of this is that Dreicor was able to partner with a lab in Tennessee to provide hand sanitizer when everyone else was out and there was a national shortage. Dreicor also dedicated, and NSG funded, full-time personnel to disinfect all high touch areas, common areas and tools, multiple times per day. Consistent messaging to the workforce and effective contact tracing were also key.
This project incorporated design-build project delivery. Now that the project is in the final phase, what are your thoughts using design-build?
One of the key selling points about using design- build for project delivery is schedule compression. I do not believe in the COVID environment that this project would be where we are without using design-build. Also, having TECO as our design- build general contractor has been advantageous, due to them being one of the glass industry’s only design-build firms in the world.
Finally, what are some of the highlights of the NSG and TECO team performance that contributed to the success of the project?
Just the fact that we got to this point with the current global heath pandemic is remarkable. From project launch, we had standing meetings with open communication of ideas, concepts, and resolutions to roadblocks. Risk assessment to the health and safety of all employees is another one. Lastly, the quality of work. So, to sum it up, the collaboration between NSG and The TECO Group is a key factor in the overall success of this project.
Add a Comment