Modeling and Simulation
Conceptualisation & Implementation of Furnace Process Design
By Kevin Fulkerson, Vice President of Technology
“Our plant will be the first to try a new process that reduces emissions, lowers operating costs, and extends furnace life without sacrificing glass quality!” How often is this statement heard in the glass industry? Almost never. The glass industry is capital intensive and risk averse. Change typically comes in small incremental steps at each repair to avoid potential mistakes and avoid resultant long-term operating issues. It is only when a design change can prove itself that it is adopted.
Sustainability is now at the forefront of the glass industry, and with it come challenges for innovation and process design. The use of Computational Fluid Dynamics (CFD) modeling provides the means to promote innovation by running many design simulations (or “what ifs”) and doing a comparative analysis to determine which changes yield the best results. The incorporation of CFD modeling in our design process is used to support and refine our empirical furnace design calculations and production-proven experience. Understanding the design process is crucial for the resultant glass quality, energy savings, lowering emissions, and extending furnace life. This design process information is vital for making managerial and technical decisions about future furnace performance.
CFD modeling and simulation provided by TECO is not limited to just the furnace’s physical design but incorporates the complete furnace melting, refining and forming temperature processes. This includes the glass space, combustion space, regenerators (if so equipped), exhausts, flues, distributors, canals, forehearths and float process tin baths. It also includes, within the glass space, the optimization of features like boost, bubblers, weirs, waist coolers, stirrers, etc.
TECO is the industry leader in glass furnace design CFD modeling and simulation. This article describes our philosophy, capabilities and the importance of conceptualizing a furnace process with the result of implementing innovative designs.
Philosophy
The philosophy behind our modeling is to make sure the client understands how the glass and combustion flows perform in their process and how we evaluate this data from comparative models to engineer the optimal solution. This always starts with creating a validated base model. A validated base CFD model is a model that accurately reflects the measured operating data from a stable time period, preferably early in the campaign life of the furnace. This validated model is the basis on which to run a series of theoretical CFD models and perform a comparative analysis. Most theoretical CFD models are based on incorporating different design features with the goal of optimizing the process. This comparative analysis is the process of reviewing the generated theoretical CFD models against the validated base CFD model.
The validated base CFD model’s degree of accuracy is proportional to the accuracy of the operating data and importantly, the glass properties on which it is based. Some of the key inputs are measured glass properties, thermocouple, and optical temperature readings with their precise locations. The CFD model’s accuracy can be incrementally improved when a high-temperature observation test is used to determine batch bubble size and the minimum fining onset temperature.
Another one of our standard practices is weekly technical reviews. These technical reviews are used to maintain the high level of TECO’s strict quality and design standards, to best enable continuous improvement and provide reliable data driven results to all aspects of the design process. This is performed by the technical team. Upon completion of technical reviews and all checking, a final presentation is created in full detail for review with the client. The complete analysis combined with the CFD model results, provides for consensus decisions by the customer and TECO.
Capabilities
TECO has been mathematically modeling since 1988. In our initial efforts, we used a 2D software application called Float Furnace Math Model, developed in collaboration with Dr. Ray Viskanta from Purdue University. Since that time, our company has expanded and invested heavily into 3D modeling and is concurrently utilizing Glass Service, Celsian and Fluent software programs. TECO is the only furnace design company in the world that runs CFD glass models using all three major CFD tools and was the first Glass Service user licensed to run tin bath models. Utilizing these sophisticated programs takes dedicated resources; our facility has 30 computers with over 1,000 cores of computing capacity reserved for this advanced industry leading capability.
TECO’s technical proficiency in modeling and simulations is supported via testimonials, and our resume includes modeling for over 45 clients with thousands of models and simulations run for their benefit. One of TECO’s clients commented, “We have been told by Glass Service that TECO is their most experienced modeler”. This accolade illustrates TECO’s detailed knowledge and advanced capability in CFD modeling.
Production Proven Results
Modeling without practical furnace design experience is ill-advised. In our 93-year history, TECO’s furnaces have never failed to perform. How has this been accomplished? By employing a multifaceted and diverse engineering staff, possessing a variety of glass furnace experience and technical specialties. Beyond design engineering expertise, our engineers have backgrounds from diverse technical disciplines and real world plant experiences. The entire TECO Group of companies worldwide share their design capabilities and training to the benefit of all companies.
Below are some examples of our CFD model studies that we have performed:
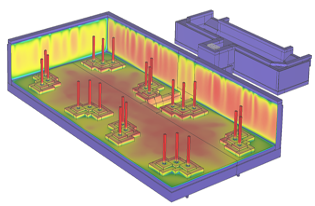
Cold Top, Slush, Hybrid
- Developed base models of cold top electric furnaces;
- Batch modeling techniques;
- Batch and glass inputs and properties;
- Electrical inputs;
- Firing patterns, phase relationship, transformer options;
- Analysis;
- Indices, glass flow, 2D versus 3D flow analysis;
- Comparison to field measurements;
- Design, refractory selection, electrode placement;
- Very deep cold top electric melter.
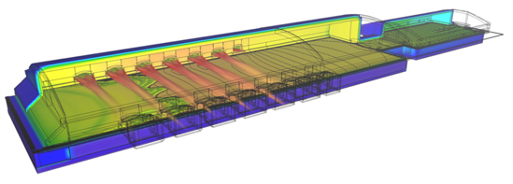
Float
- Furnace optimisation;
- Operational set points for fuel flow, cooler depth;
- Glass distortion analysis to remove centerline distortion;
- Glass flows match carbon flow studies;
- Refractory flow patterns match those predicted by the model;
- Boost, bubbler, cooler and step optimization;
- Bubble and seed trajectories;
- Low Fe, dark glass;
- NOx reduction;
- Furnace bottom temperature analysis;
- Glass quality versus design change;
- Defect analysis;
- Shear analysis.
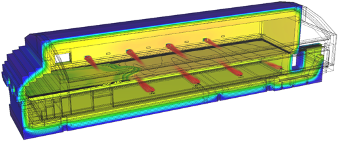
Oxy-Fuel
- Base furnace;
- Optimize burner height;
- Batch dust;
- Optimise boost;
- Optimise bubbler location;
- Optimize throat;
- NOx reduction;
- Exhaust temperature and velocity optimization;
- Glass quality versus design change;
- SLS glass, E-glass, C-glass, specialty glass;
- Furnace bottom temperature analysis;
- Defect analysis;
- Shear analysis;
- Boost and bubbler optimization;
- Bubble and seed trajectories.
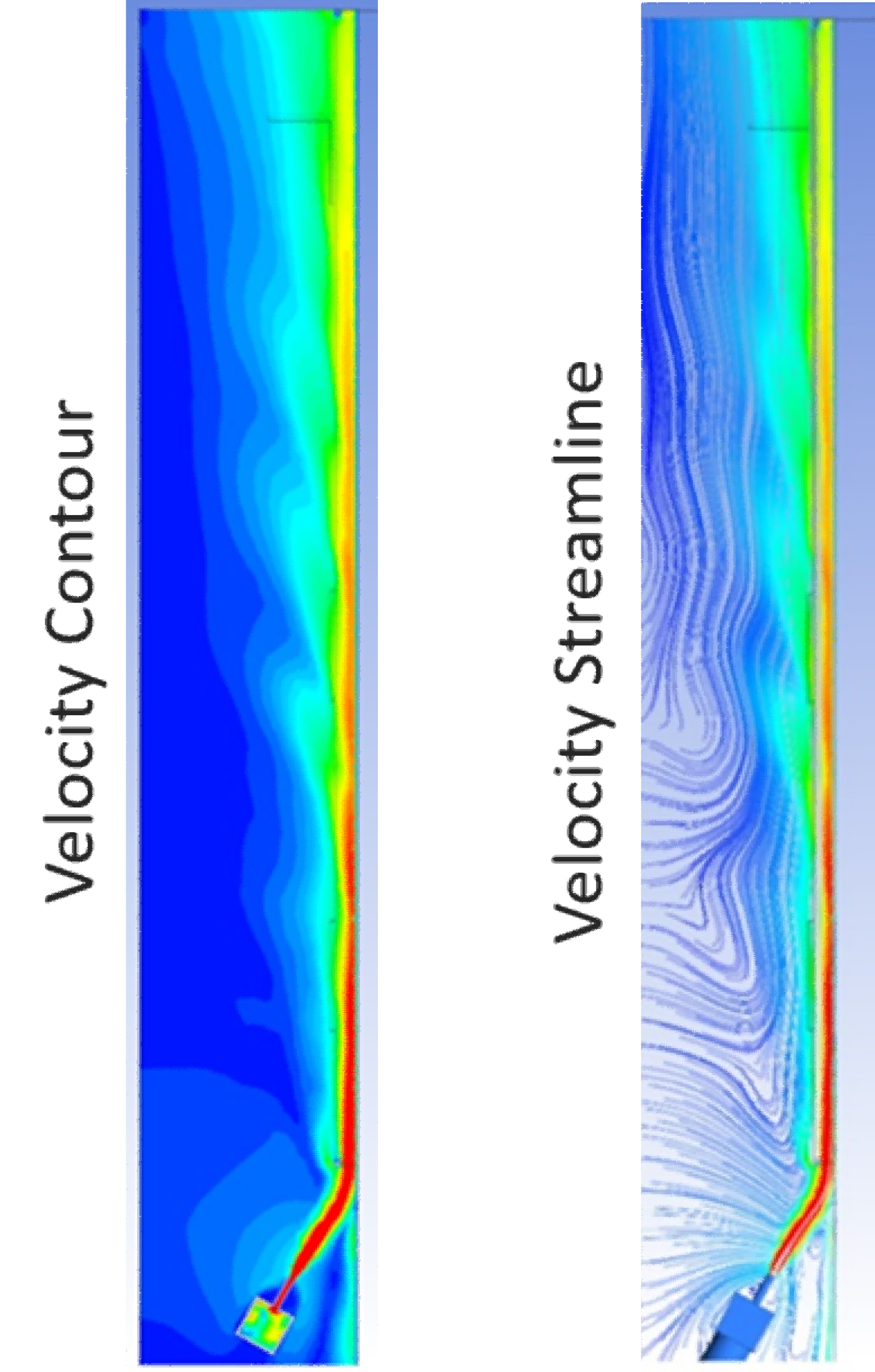
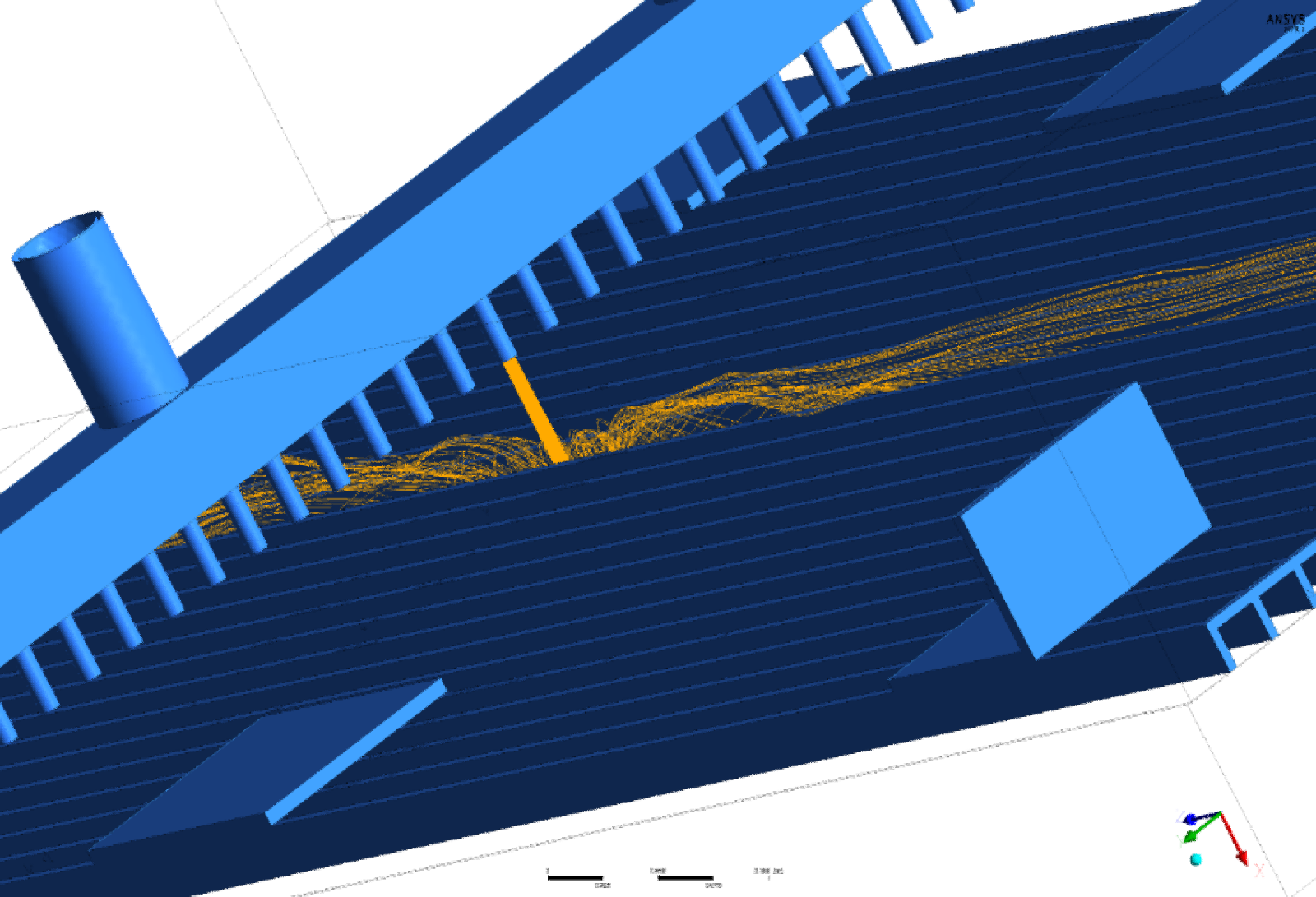
Sidewall Cooling Using Fluent
Sidewall cooling wind analysis to locate cooling wind nozzle angle and placement to maximize cooling.
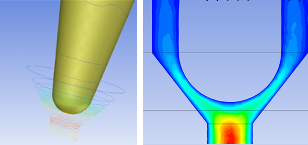
Predicting Glass Flow through an Orifice Using Fluent
Study of methods to control flow through an orifice based on size and plunger.
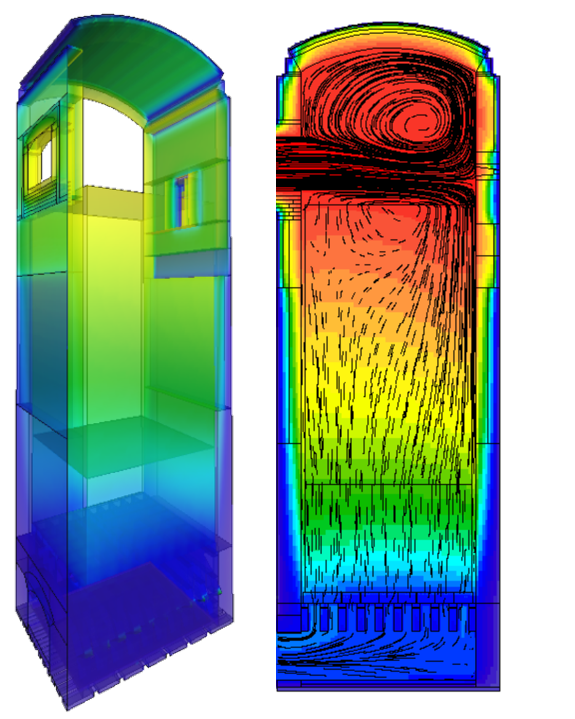
Regenerators
Developed multiple end port and float furnace regenerator models for:
- Validation studies;
- Checker pack optimization;
- “C” vs. “S” combustion flows;
- Air dampening;
- Shadow wall;
- Upper & lower chamber optimization;
- Refractory design optimization;
- Checker vs, porous media studies.
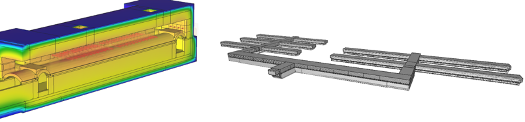
Simple, Complex and Muffled Canals and Forehearths
- Design of the world’s largest E-glass furnace;
- Optimized oxy burner layout and flows;
- Optimized FH zone firing.
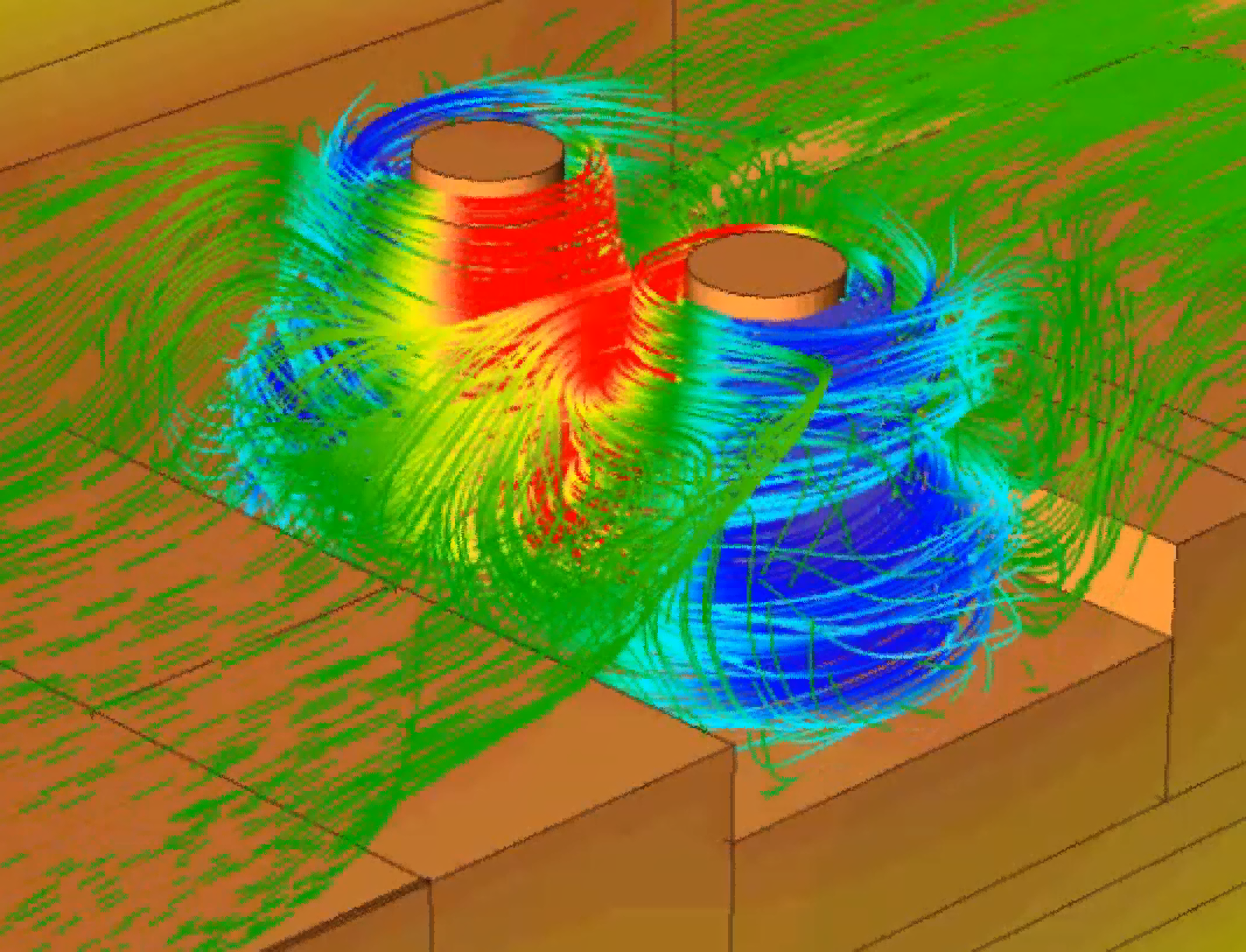
Transient Modeling
- Optimization of stirrers by type, rotation and location;
- Optimization of canal dimensions.
Conclusion
TECO’s modeling and simulations are recognised by the glass industry as world class. This is due to our full range of capabilities and production proven results. Our customers benefit from our furnace design capabilities and multi-facetted range of CFD modeling programs. Our models are not simply run by modelers but by experienced engineers that understand and design the entire furnace process and can provide complete explanations when the results are presented. As seen by the examples above, our modeling and simulations are extensive. TECO’s guiding modeling principle is to produce an optimal solution in detail, which can be fully understood by the customer enabling them to make the most informed decisions, utilising world class technology, to give them a world class glass process.
Add a Comment