FEL IN A WELL
The Risk of Performing Front End Loading Without the Benefits of Engineering and Construction Collaboration
By David Bennert, Vice President of Project Management
Conducting a Front End Loading (FEL) process without the support of experienced engineering and construction participants is like ‘conducting a FEL in a well’. Does your team have the capacity and the experience to conduct a FEL, or are they working in isolation, i.e. are they working ‘in a well’?
WHAT IS ‘FRONT END LOADING’?
Front End Loading is not a new concept, but it is gaining the attention of smaller companies as stakeholders demand more credibility related to capital spending. The Front End Loading process was developed by the Dupont Corporation in the 1980s in response to a congressional directive for the Department of Energy (DOE) to establish a more disciplined approach to project development, execution, and review. In other words, Congress did not trust that the DOE or the operators of the DOE facilities were critically managing projects to optimize value and minimize cost overruns. As a result, Front End Loading (FEL) was created.
Front End Loading is defined in a variety of ways, from both a performance perspective and a process perspective. A performance definition states, “….FEL means you define what it is that you want to do in such a way that the people who are going to do It can carry it out in the most business-effective way (James B. Porter, 2002).” A process definition provides further clarification by stating “FEL refers to a project management process that involves developing sufficient project definition so that the owners can make investment decisions, minimize risk and maximize the potential for success. (Construction Industry Practices Guide, 2012)”
The concept of Front End Loading is summarized in Figure 1, below:
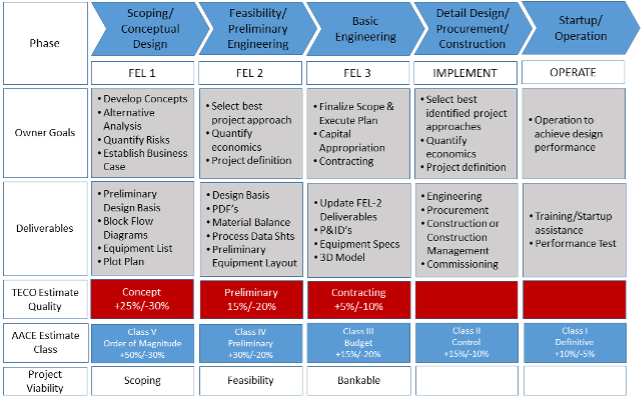
Figure 1: Front End Loading Definition within Project EPC Structure
FEL QUALITY: TIME AND RIGOR
One of the single most important requirements of the FEL process is time. To ‘front end load’ a project, the FEL process should begin far enough ahead of the detailed engineering and project execution schedule to allow each FEL outcome to be presented, reviewed, and challenged, and adjustments made before moving on to the next FEL level. The schedule must allow sufficient time to respond to each FEL deliverable, by either changing the business case (e.g. capacity, concept), the design (e.g. preliminary scope, alternative analysis), or the front-end engineering (e.g. preliminary design, specifications, procurement plan), or other project attributes. The amount of time required for the FEL process is commensurate with the complexity of the project and the deliverable package for each step of the FEL process. The sample schedule in Figure 2 below gives some indication of what is required for a major project, and how the FEL process interfaces with bidding, final budgeting, project authorization, and execution.
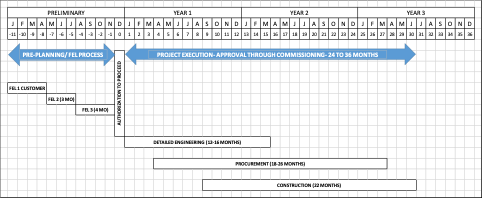
Figure 2: Sample Schedule- Schedule Optimization During Front End Loading
Even though the FEL process is more typical in a design-bid-build execution format, the principles can still be applied to fast-track design-build projects, though the benefits of the FEL process may be diminished. If the owner is committed to the FEL process and is willing to commit the necessary technical resources, the project outcomes can be improved. Figure 3 below indicates how the commitment to the FEL process relates to the value gained. To achieve the maximum benefit from the FEL process, time commitment and rigor are proportional to the outcome. This is even true of the early stages of the process which should consider the quality of the business case, alternative analysis, cost estimates, schedule risk realization, etc.
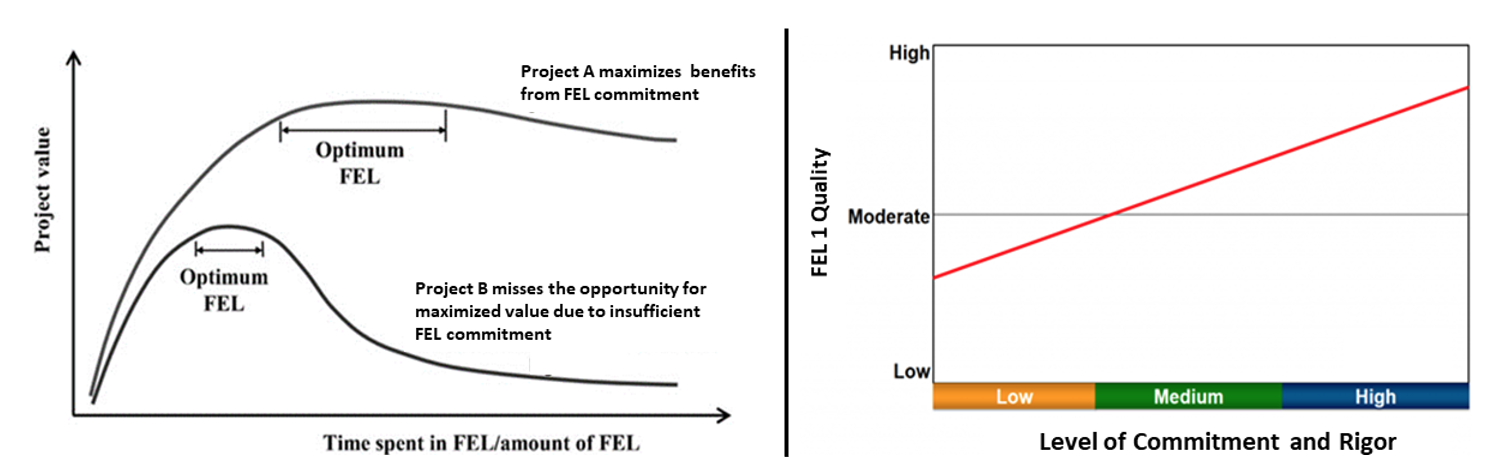
Figure 3: Relationship Between FEL Commitment and Attaining Project Objectives
If opportunities for project improvements exist, identifying and acting on them early in the process (e.g. during the FEL process) is critical to controlling project costs. So, this begs the question, “Does your engineering and operations teams have the time to carry out the FEL process with sufficient rigor to maximize the value of the FEL?” With the need for ongoing operations support, very few glass producers have excess capacity to conduct thorough assessments at the FEL 2 and FEL 3 stages. This is where having partnerships with qualified engineering and construction teams becomes critical to producing a quality FEL analysis.
WHY THE FEL TEAM IS CRITICAL
The FEL process is owner-driven, which implies that the owner is responsible for developing the team with the right blend of skills to provide value-added input to the process. To successfully carry out the FEL process, the team must consist of individuals familiar with the execution of all phases of the project. The owner is usually capable of providing knowledge of plant/process operations, process engineering, and product-specific cost estimating. These talents are crucial to developing the business case and project concepts, and are critical to the FEL 1 stage of the process.
But if the project involves major facility/process modifications, repairs, or expansions, does the plant team have the knowledge and experience in equipment design, fabrication, transportation, erection, building construction, HV/MV power distribution, procurement of specialty components, and construction safety and scheduling? How many major capital projects has the owner’s team executed? Are they familiar with the current construction codes and safety requirements? Are they staffed to support the FEL 2 and FEL 3 requirements? The FEL 2 and FEL 3 process requires additional skills of engineers and contractors with experience related to the detailed design and construction of the project. Figure 4 describes the stages of involvement of both the owner and the contractor.
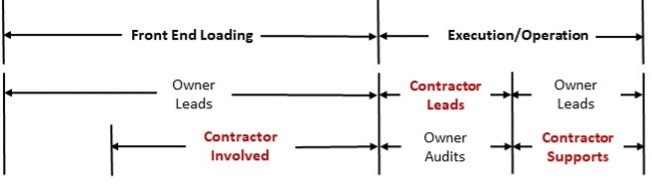
Figure 4: Project Roles and Responsibilities
An excerpt from an article by Suresh Kumar of McDermott Industries states it best;
Some main causal factors inherent in poor Quality FEL process are “time pressure due to market conditions, not enforcing the compliance to requirements, lack of qualified engineers and subject matter experts, failing to promote creativity or innovative solutions, etc.,” which may require us to invest in quality assurance of the early pre-project planning process.
In short, the benefits offered by the FEL process are directly related to providing sufficient time for the FEL process to occur, having the proper blend of skills and experience, and committing to the rigor necessary to optimize the project scope and variables.
When assessing the benefits of the FEL process, consider this:
The Lang Factor is an estimating technique that is recommended by the American Association of Cost Engineers (AACE) for Class 5 and Class 4 estimates (roughly corresponding to FEL 1 and FEL 2). The Lang Factor that is applied for projects involving solid product manufacturing (e.g. glass manufacturing) estimates that the total installed cost of the plant is approximately 3.10 X the cost of the purchased process equipment. That means about 65% of the project cost is tied up in detailed design, structural steel, piping, electrical, insulation, painting, construction labor, and project and safety management. Does the plant operations and management team have experience in these areas?
So, this is where having team members with in-depth knowledge of the engineering process, process-specific procurements, fabrication, construction, and construction safety become critical to the success of the FEL.
TOLEDO ENGINEERING CO., INC. (TECO) has been designing furnaces and hot end process equipment for over 90 years. During this time, they have designed over 1000 furnaces. Engineering tools used by TECO include computerized fluid dynamics (CFD) modeling, 3-D design software, project estimating software, cost models, and scheduling software. These are the tools that should be applied to allow concepts to be developed, viewed, critiqued, revised, and refined- all of the key functions of the FEL 2 and FEL 3 process. These are the same tools that provide the rigor necessary to challenge and optimize the design, budget, and the overall project plan.
DREICOR, INC., the construction arm of the TECO Group, has been providing fabrication and construction services to TECO and the glass industry worldwide since 1979. This includes new construction, maintenance, and repair of all types and sizes of furnaces- regenerative, recuperative, gas-oxy, boosted, cold-top electric, and even some unique furnaces utilizing plasma heating. DREICOR takes responsibility for both the fabrication and the construction roles and is intimately familiar with the labor requirements, staffing levels/staffing schedules, safety requirements, and the sequencing of work required to optimize new construction or cold repairs.
Does your plant have these talents? Aren’t these the skills required to properly develop your project?
COST/BENEFIT CONSIDERATIONS
The FEL process generally accounts for about 2-5% of the project’s total installed cost (TIC). It’s important to note that the 2-5% allowance includes a significant portion of the engineering. By the time the FEL 3 process is completed, about 30% of the engineering is also completed, which includes the selection of major equipment and suppliers. If the FEL process is followed with rigor, the necessity for contingency is reduced at each step of the FEL. Referring back to Figure 1, by the completion of FEL 3, Class 3 cost estimates have an accuracy of +20%/-15%. This correlates to a possible budget shortfall of 20%, or a contingency requirement of 20% of the TIC. TECO’s budget accuracy after FEL 3 is typically around +5%/-10%, which warrants a much lower contingency allowance of about 5% of TIC.
Under conventional contracting without the benefit of the FEL process, the bidders list is down-selected to a qualified group (i.e. safety performance, financial stability, quoted/estimated price, etc.). From that point, the vendor is generally selected based on the best-negotiated price. The accuracy of the negotiated price is commensurate with the quality of the bid package and engineering to date. Without the benefit of the FEL, there is an increased risk that the budget will not be met, and the schedule exceeded, and both conditions will not be realized until project execution is underway. Changes to the project once execution is underway result in the largest cost variances and schedule impacts. Figure 5 below tracks the impact of late decisions, and emphasizes the fact that changes made after the FEL process can be orders of magnitude costlier than change made during the FEL process.
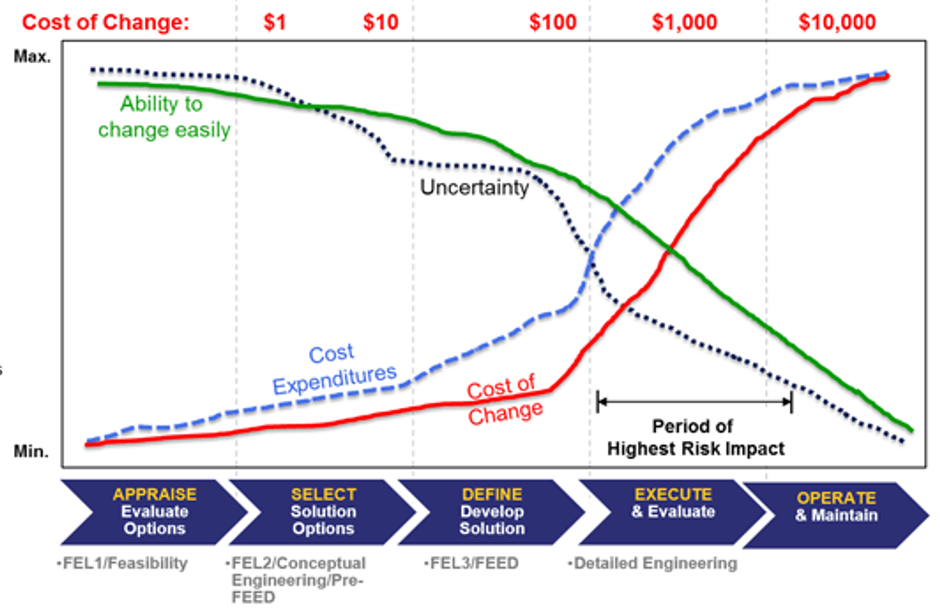
Figure 5: Project Phases
If you ‘overlay’ the roles in Figure 4 with the graphic in Figure 5, you can see that the engineering group and the construction contractor directly impact the FEL 2 and FEL 3 phases. The drop in the uncertainty at the later stage of FEL 3 occurs at the same time as the abrupt increase in project cost associated with design/project plan changes. The cost impact is even worse as the project enters the execution phase. After completion of the FEL 3, the design (should be) locked, with the equipment specified and ready to order. Changes, even minor ones, have a trickle-down effect and must be incorporated into the design. All impacts and interactions must be assessed, and the necessary changes made to all affected documents (i.e. re-engineering work that is already completed). Regardless of how small the change might be, time and resources are expended, including engineering, procurement, project management, and administrative personnel.
TECO and DREICOR address these needs. Design development during the FEL 2 and FEL 3 periods includes the establishment of the design basis, development of the PFDs, process data sheets, P&IDs, process layouts, equipment lists, equipment specifications, and 3-D models. Throughout these phases, cost estimates and schedules are refined using the experience of the construction contractor. These tasks are key to reducing unknowns, refining the project plan, and reducing financial and schedule risk.
Figure 6 below sums it up. Good project definition in the FEL phases sets the project on a path to maximize value. Even if execution falls short, the benefits of proper planning will still be realized.
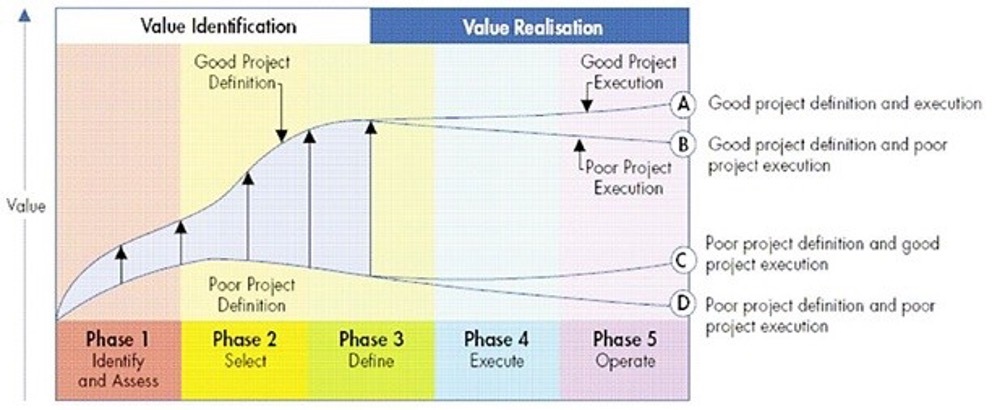
Figure 6: FEL Value Identification and Realization from Inception to Operation
So, what does this mean in terms of project performance? Does the process produce the benefits to justify the additional cost of the FEL? The answer to that depends on your perspective on cost overruns and schedule attainment.
Projects can be planned and budgeted to include large contingencies. But contingencies are intended to cover unknown costs in a project. So that translates into the following: 1) you do not know the project scope, and 2) you do not know the project cost. By inference, you don’t know your schedule either. And you won’t have a handle on the project cost or completion schedule until the project is completed. Figure 7 below shows the FEL performance as it relates to estimating project cost. The industry norms at various stages of the process are presented in black, and compared to TECO cost estimate performance in red. TECO performance generally reduces the overestimation of the project, and reduces the uncertainty significantly by the time FEL 3 is attained.
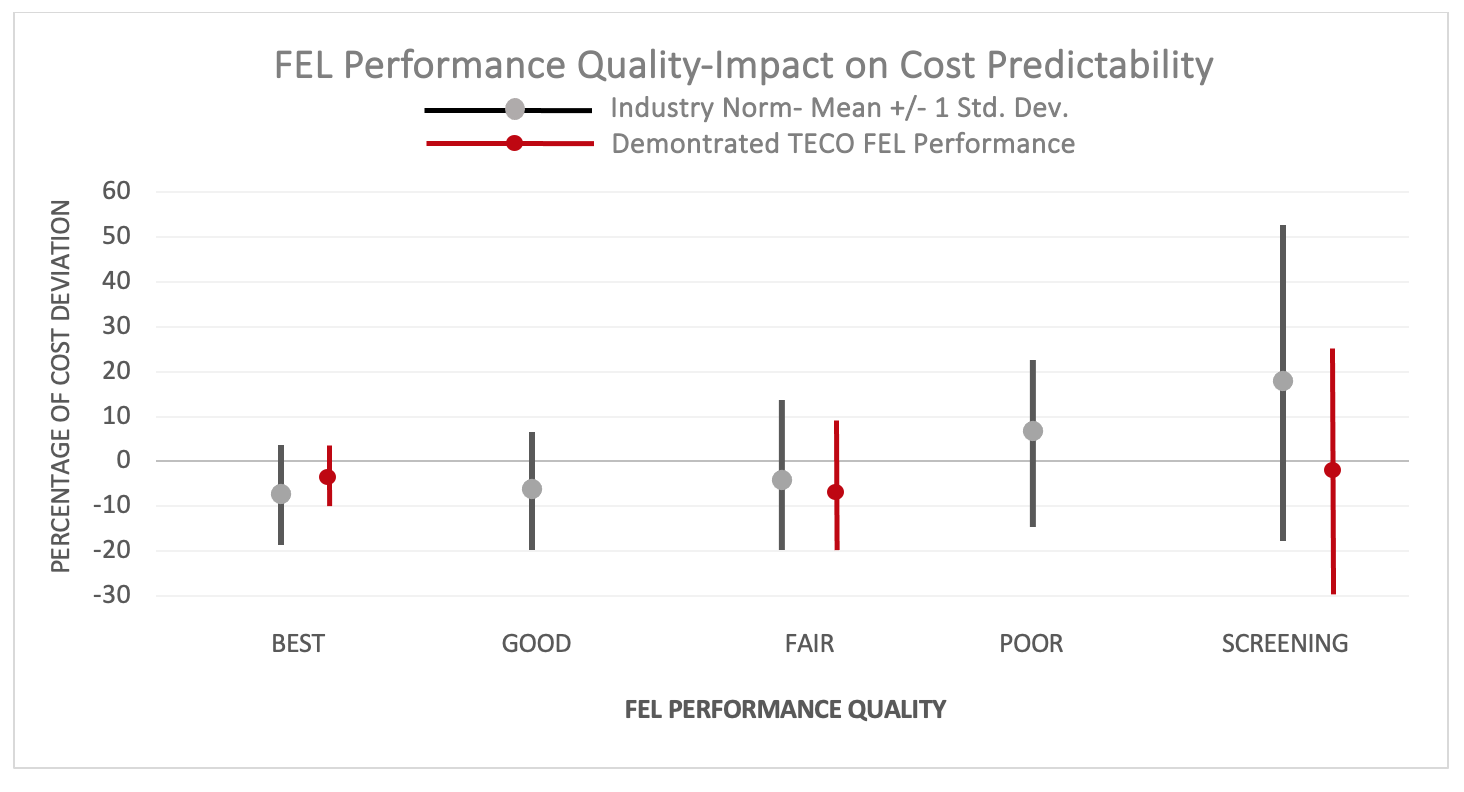
Figure 7: FEL Performance Quality Impact on Cost Predictability (TECO versus Industry Norms)
The application of contingency may address the unknown aspects of the project scope and budget, but the magnitude of the contingency can directly impact the feasibility of the project. The ROI is based upon an assumed TIC. For large capital projects, contingencies skew that analysis by making the project more or less profitable, depending on the contingency plan. Large contingencies may ensure that the project can be completed within budget, but they can also reduce the project viability by reducing the anticipated profit margin.
Construction schedule attainment responds to FEL performance in a very similar manner as cost predictability. The FEL quality improves the engineering cycle as well as the construction schedule, contributing to the overall schedule improvement. The increased rigor of the FEL process reduces the schedule variance 15-17% over poorly planned projects, and about 10% better than industry average overall. The schedule benefits of the FEL process is presented in Figure 8 below.
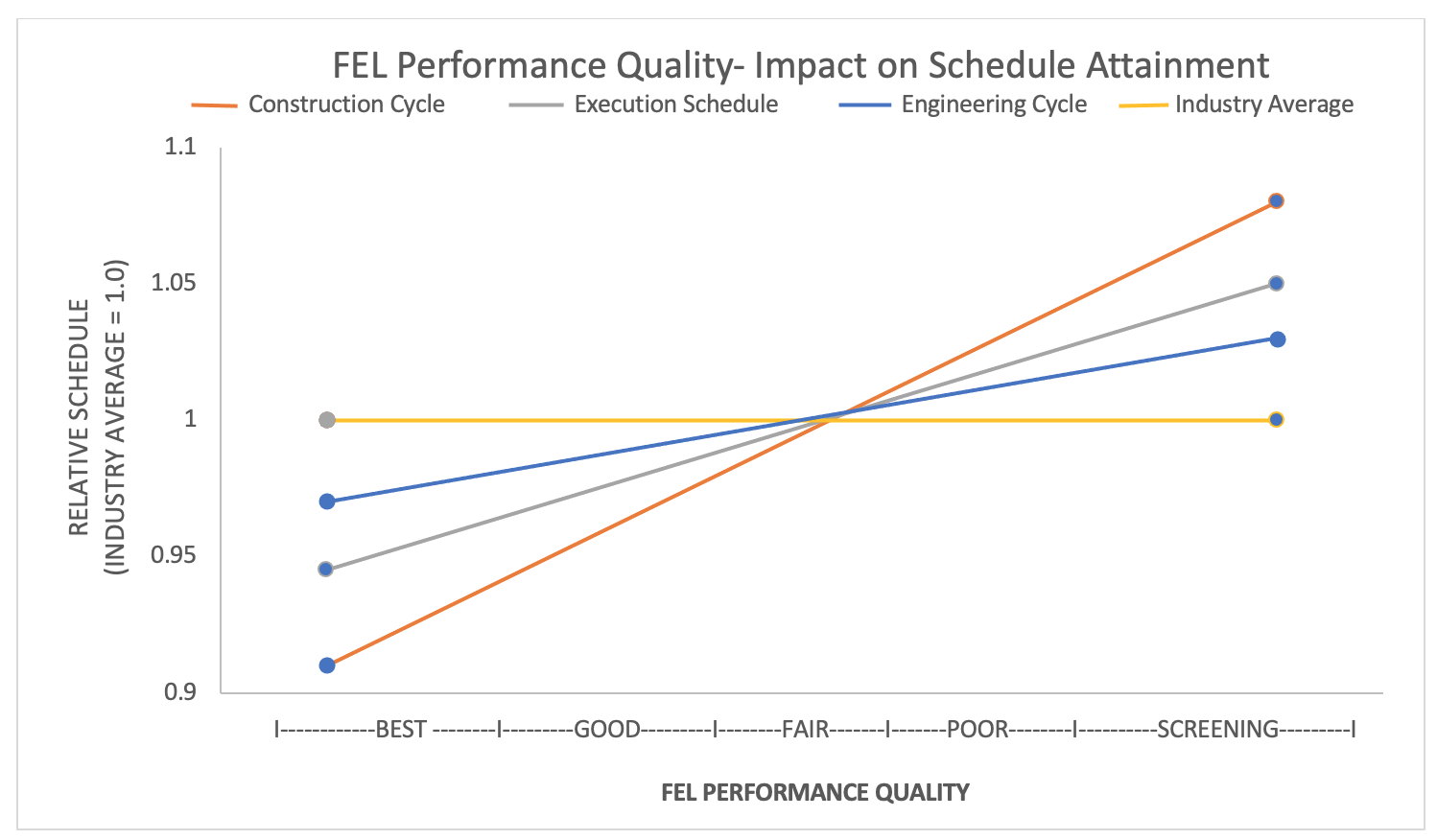
Figure 8: FEL Performance Quality Impact on Schedule Attainment.
So, can an organization that is focused on plant and process operation reasonably develop its business case without having expertise in engineering, procurement, fabrication, and construction of a plant or process line? Not likely. The structure of the FEL team is critical because it must have the disciplines skilled in all aspects of the project in order to provide the rigor necessary to produce an accurate outcome. This is where the engineering experience brought by TECO, and construction knowledge brought by DREICOR become critical to a successful team and FEL outcome. This translates into:
- A very high confidence level that the project cost will be between +5% and -10% of the target budget, or in simpler terms, that the project will come in under budget.
- A very high confidence that the project will meet the projected schedule, with a high probability that it will beat the schedule.
- A high confidence that the project outcomes will align favorably with the business case, including capacity, capital investment, and schedule/time to market.
HOW DEEP IS THE WELL?
The best well is one with a plentiful source or supply- in the case of an FEL process, a supply of experienced engineers and construction experts is critical. Luckily, to mitigate risk, engineering and construction experience is available through TECO and DREICOR. The TECO Group is uniquely positioned with the resources to properly supplement and support your team for the FEL-1, FEL-2, and FEL-3 processes. Plus, the well goes deeper because The TECO Group has the full engineering, procurement, and construction resources to carry the FEL 3 outcomes through the procurement, construction, and commissioning stages.
Conducting a ‘FEL in a well’ is equivalent to working in isolation with only half a team, and expecting a high quality outcome. Producing FEL deliverables without in-depth, experienced engineering and construction knowledge will not provide the rigor necessary to ensure that your project fulfills the business case, let alone gain the benefit of reduced cost and schedule risks. TECO and DREICOR can provide the experience needed to complete your team, and maximize the benefits of the FEL process.
Add a Comment