Radiant Heating Systems In Glass Applications
Radiant heat is employed in many sectors of the glass industry to control cooling of a material during the part of the process where direct contact of the glass is not viable. The use of radiant heat covers a large range of temperatures and often requires a large band of power control for the heating process. Typically, during startup, a large amount of heat is required in the application. In normal operation, however, only 20% to 60% of the startup heat is required. These large swings in power usage generally come with higher costs from electrical losses due to the broad range of control required.
Typical control methods used in the glass industry today include the Silicon Controlled Rectifier (SCR, also known as a Thyristor) and the Saturable Reactor. SCR controls limit power by using “phase angle control” to reduce the on-time of a natural Alternating Current (AC) sine wave. When an SCR is scaled back to less than 60%, power delivery is less efficient due to harmonic and displacement content. This results in more expensive energy from power factor penalties and higher peak demand. Shockingly, these SCR power systems will spend most of their life in this reduced, inefficient state. With a Saturable Reactor, power is applied to the reactor to magnetically limit the power delivered to the load. This is lost power because it used by the control system and not directly applied to the process.
More efficient radiant heat can be produced by an equivalent Direct Current (DC) power supply. Herein, we describe an analogous comparison of radiant heat between a traditional AC system with an SCR and a DC system with an IGBT/MFDC system. An IGBT/MFDC system utilizes an IGBT control (Insulated-Gate Bipolar Transistor) and MFDC (Mid Frequency Direct Current) transformer. An IGBT/MFDC control system uses all three phases of the power grid and converts standard AC to a square wave output at medium frequency. The square wave is sent into a specifically designed water-cooled transformer with an integrally mounted rectifier to output a low ripple content DC waveform to the process. The increased frequency of the square wave reduces the size and weight of the transformer. A schematic of the system is shown below.
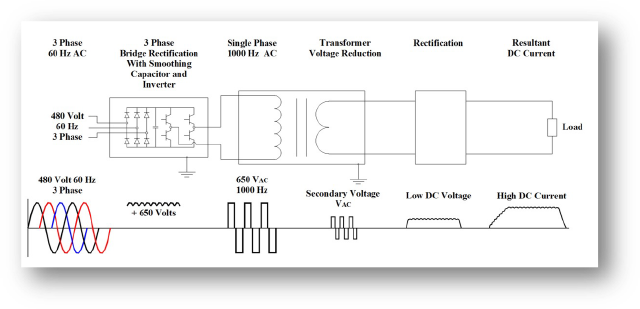
The major advantage of a DC power supply is that inductance, or coupling losses, is practically eliminated. Direct current has no frequency and subsequent inductance. This creates a high-power factor on the front end of the system. The IGBT/MFDC system has a high DPF (Displacement Power Factor) across its control range. This also contributes to reduced power factor charges in utility bills. Other utility charge improvements include Real Power (kW), Reactive Power (kVAR), Total Power (KVA) and Peak Demand.
Radiant Heat Comparison (AC versus DC)
The experimental goal of this study was to measure radiant heat in a controlled environment with heating elements typically used in the glass industry. Does radiant heat differ from an AC versus a DC power source?
The experimental setup is shown below. A Kanthal heating element was powered in a controlled environment. Thermal characteristics were measured at specific points to compare the heating patterns of AC and DC power supplies. Measurements were taken with both thermocouples and IR readings. Locations for the test points are shown in the ‘Top View’ and ‘Front View’ diagrams below. A variable transformer was used in single phase operation for AC testing. A bridge rectifier with single phase output was used for DC testing.
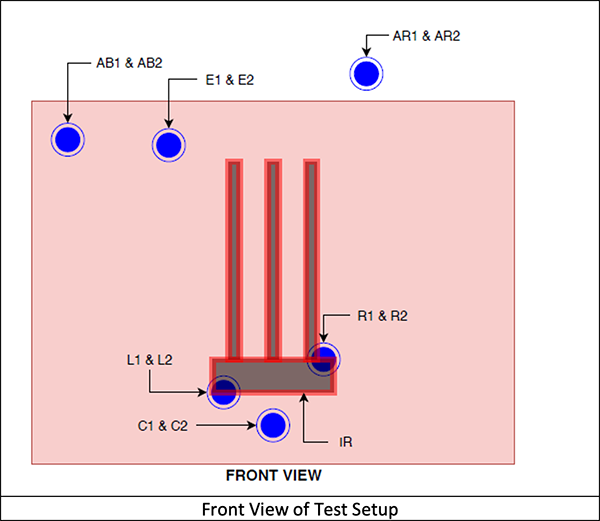
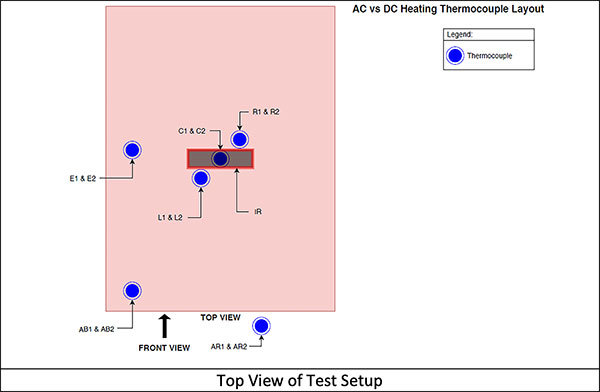
The current was controlled in both AC and DC systems to 75 amps across the heating element. Thermal measurements were concluded when thermocouple and IR readings had a less than 5°C change over a 30-minute period of time. Ambient temperature and other environmental factors were controlled to provide an accurate comparison.
Results:
In the chart below, the data shows that AC and DC current create approximately the same amount of heat inside the controlled environment. This demonstrates that DC power is at least equivalent regarding thermal characteristics in radiant heating applications. This thermal equivalency predicates the myriad of other power benefits that DC power offers.
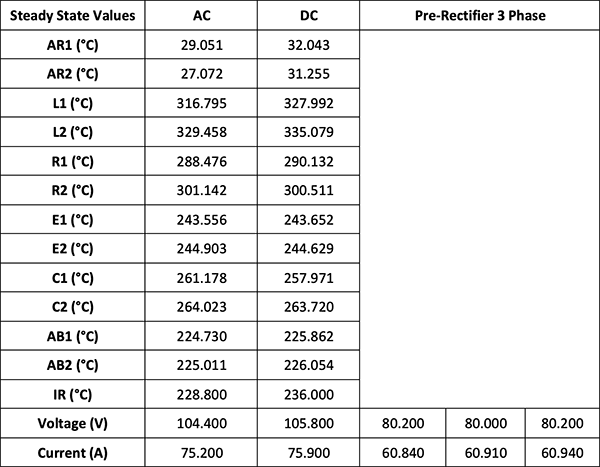
Advantages of an IGBT/MFDC system include:
- Smaller transformer size due to the increased frequency
- The smaller water-cooled transformer can be located closer to the load eliminating transmission losses in the system
- All three phases of the power system are used reducing any imbalance issues in the facility
- Utility costs (operational expenses) in terms of Real Power (kW), Reactive Power (kVAR), Total Power (kVA) and peak demand can be reduced
- Displacement Power Factor (DPF) is increased reducing Utility costs
IGBT/MFDC systems are being used in other industries such as the Industrial Furnace and Resistance Welding marketplaces due to the benefits listed above.
Currently the Glass marketplace utilizes Variable Frequency Drives (VFD) in segments of the process which share similar components to the IGBT system demonstrating that this technology is viable in a Glass manufacturing facility.
Please contact us if you would like to discuss the usage of an IGBT/MFDC system in your application.
Authors: Stanley F. Rutkowski III, Senior Applications Engineer (email: srutkowki@romanmfg.com Phone: (616) 530-8641) and David Pridmore Applications Engineer (email: dpridmore@romanmfg.com Phone: (616) 530-8641) both from RoMan Manufacturing Inc. Grand Rapids MI, USA www.romanmfg.com
Add a Comment