Pursuit of Technology Balance
A Three Part Series of Melting Characteristics – Part 1 Backwalls
By: Tim Park, Vice President - Merkle International
From the Editor’s Desk
Technology is defined as the science or knowledge put into practical use to solve problems or invent useful tools, or a manner of accomplishing a task especially using technical process, methods or knowledge. Balance is defined as the equilibrium between contrasting, opposing or interacting elements. At TECO, our Technical Team is continually designing the world’s optimal furnace solutions utilizing the optimal design and engineered practices from the entire glass industry. We, at TECO, call this the Pursuit of Technology Balance.
Over the next three issues of Glass 5.0, we will be covering different areas or features of a furnace to compare and contrast technologies and design. The three areas to be covered will be the backwall, weir walls and throats. Our aim is to prompt readers to contemplate the relevance of these features and ask questions such as, does it make sense? Does it fit within the goals of a glass company, such as consistent growth and produce quality glass through continuous innovation? Is it simple by design? and most importantly, does it add value and reduce my total cost of ownership?
In the first of the three part Glass 5.0 series of articles, Tim Park writes about the Merkle backwall and the value of engineering and design that it brings towards a technologically balanced furnace solution.
All feedback is welcome, as well as any suggestions for future articles, and please visit TECO and myself at our table top booth at this year’s Glass Problem’s Conference in Columbus. I hope you enjoy this issue.
Brian J. Naveken
Introduction
Backwalls are an essential component of a glass furnace, especially on wider designs. They are responsible for containing energy within the furnace, while providing an even gap for charging the furnace. Backwalls must survive high temperatures and a corrosive environment, despite the temperature differences and batch dust at the feed end of the furnace. Some furnaces can also employ flue exhausts near the backwall.
What is a Merkle Backwall?
The backwall is a suspended refractory construction, with integral support steel, cooling air and specialty refractories. The goal is always to match the refractories to the furnace design and campaign requirements.
Today’s modern cross-fired furnaces have pull rates of 600 -1200 tons per day. These pull rates are too large for end-port furnace designs, so cross-fired furnaces are usually chosen. A properly designed Merkle backwall can cover the entire backwall, leaving the aformentioned constant charging area. Figure 1 shows a common suspended backwall with different refractories in different sections of the wall.
Typically, there can be temperature variations due to furnace and batch upsets. The resulting thermal shock can rapidly degrade refractories. Certain bonded alumina-zirconia-silica (AZS) refractories can be a solution to thermal shock problems. Higher on the wall, vapor attack is a greater threat, so other refractories are chosen. Finally, silica refractory can be used in the vertical section, matching the silica furnace crown materials. Merkle backwalls are routinely part of campaigns of 15-21 years.
The refractory system is hung over the furnace feeding pocket, or doghouse, supported by an air-cooled steel structure. The Merkle system has unique designs for adding insulation to the wall, recovering the insulation capital costs in a few months or a year.
Future
Oxy-fuel furnaces can have flue gas exhaust ports near the backwall, which adds complexity to the furnace design and requires specific refractory selection. Hybrid melters, incorporating high levels of electric boosting, and/or changing energy inputs will mean a different set of thermal and operational demands. If adopted, hydrogen firing will introduce higher concentrations of water vapor, placing an additional demand on furnace refractories, including the backwall. Merkle has been designing and supplying unique suspended refractory systems for over 50 years, and are up to the challenges that these new furnace designs will bring.
Analysis: Merkle Backwall vs. Twin-Doghouses for an Oxy-Fuel Furnace
Merkle has supplied many backwalls and blanket batch chargers over the years. Through a high number of empirical observations, we see that the insulated wall improves melting and reduces batch carryover. We do not have two identical furnaces, with identical raw materials and operating conditions to make a 100 % comparison. However, with today’s computational fluid dynamic (CFD) furnace modeling, just such an analysis can be performed. Does a furnace with a Merkle backwall perform differently than a furnace with a double-arch construction? Two identical 600 metric ton per day oxy-fuel CFD models were performed. The first model had two batch chargers with a rear exhaust, while on the second model the backwall was replaced with a suspended style backwall with a full width doghouse.
The results of the testing are shown in both graphic and tabular forms:
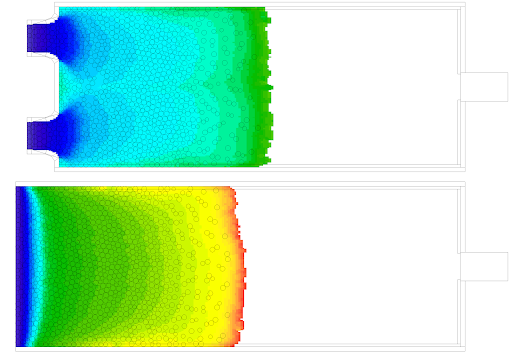

Figure 2: Batch at glass line
Figure 2 shows a side by side comparison of the batch coverage and temperatures at the glass and batch interface.
The results of the analysis were strikingly clear, that the furnace with the Merkle backwall provides superior performance. From a glass standpoint, the advantages of the design using a suspended backwall are (Fig. 3):
- The average glass temperature is 2.1 °C higher (better heat transfer efficiency);
- 4.48% to 11.81% increase in residence time;
- 4.62% to 19.82% increase in the fining indices;
- > 6% improvement in the melting index;
- A 3.3% decrease of bubbles leaving the riser;
- No wear at the doghouse corners (results in less expensive refractories and much less hot work maintenance).
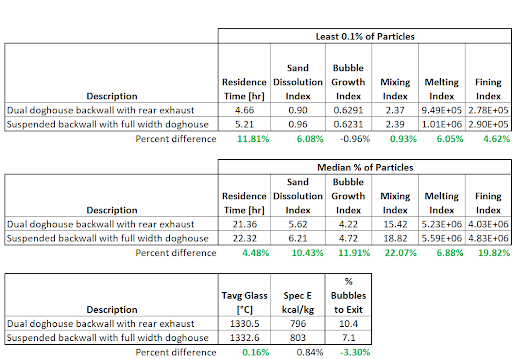
Figure 3: Modeling indices comparing furnace designs
From this modeling comparison, the effects on the batch due to a suspended backwall are as follows:
- Reradiation of the backwall puts energy/temp back into the batch;
- The batch average temperature was 221 °C higher;
- The dual doghouses have an uneven batch development or delay in batch melting. This can easily be seen by the dead zone between the doghouses.;
- Unwanted batch travels farther downstream in the dual doghouse model;
- More consistent batch temperatures from side to side and back-to-front.
Merkle Backwall and Full Width Doghouse Advantages
While we were pleased to see our general observations confirmed through rigorous CFD modeling, the underlying furnace design consequences were not 100% clear. It stands to reason that you will have maximum radiative heat transfer between the cold incoming batch and the hot backwall surface. The temperature driving force is: Th4-Tc4, so heat flux is maximized when the bodies have the greatest temperature difference. Radiative heat transfer is also dependent on area. If we have more batch area and more backwall area just above the batch, heat transfer will be higher. Merkle knows that furnace designers value the insulation package for thermal efficiency. They also value the sloped nose for radiant heat transfer to the batch. Frank Miller, Director of Field Operations at TECO, said, “Radiant heat is critical at the doghouse. It starts the melting process and glazes over the batch to help reduce carry-over. The furnace design is critical and the TECO design is world-class.”
For a deeper explanation, Frank explains:
“A TECO standard full width doghouse allows for ideal convection flow development which results in better overall melting and glass quality. Merkle blanket chargers are biased to control the batch coverage to provide an even and consistent log-style blanket, instead of an inconsistent batch pattern (Fig. 4), which can have propensity of migrating or straying too far down tank. A logged batch blanket has more surface area, therefore, more melting area and puts the batch in the middle of the tank where most of the energy is concentrated (Fig. 5). This also results in reduced sidewall wear. A wider, thinner batch area results in better heat transfer, which equals better efficiency, better yields and lower emissions.”
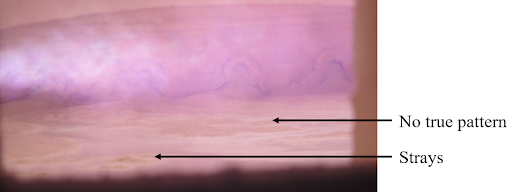
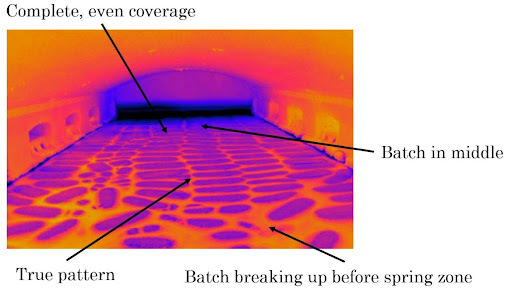
“The end result is better heat transfer, batch glazing and melting and ultimately better quality and furnace life.”
Conclusion
With the current tendency towards larger furnaces, both cross-fired and oxy-fuel, a Merkle suspended backwall is the correct choice for technologically balancing the optimal furnace for energy consumption, emissions, extended life, and continued high glass quality resulting in high customer satisfaction.
Add a Comment